maxon motors - Configure high-speed drives from your sofa
Never before has it been this simple to put together a customized, high-end drive, at work or at home, using maxon motor's online configurator. A variety of brushless, high-speed motors and gearheads are now available.
The maxon configurator is expanding its offering.
Never before has it been this simple to put together a customized, high-end drive, at work or at home, using maxon motor's online configurator. A variety of brushless, high-speed motors and gearheads are now available.
When constructing a prototype, or if a product is scheduled for a rapid market launch, it is often necessary to choose the right DC motor for the project very quickly. In such cases, engineers go to maxon motor's online configurator. The platform has tens of thousands of drive options to choose from, all of which are available quickly and easily. In addition to the brushed and brushless DC motors with diameters of 8 to 35 millimeters available in the configurator, maxon recently expanded its range of brushless ECX drives.
As a result, ECX SPEED drives are now available in a variety of sizes, both in the high-power or sterilizable versions and also with the option of ceramic bearings. In addition, we offer planetary gearheads (GPX SPEED) to complement the ECX drives and, as a sealed design, tolerate 2,000 autoclave cycles. The entire range of products available in the configurator can be found at: shop.maxonmotorusa.com
Ready in only 11 days
The online configurator, allows users to assemble their individual drive including: shafts, flanges, electrical connections, etc. This gives users a whole new range of possibilities. A complete drive - including gearheads and encoder - can be configured and ordered in only a few minutes. The electronic data goes directly to maxon motor's production facilities, where the drives are put together in automated processes. Once order is placed, it will be processed and shipped within eleven working days.
Featured Product
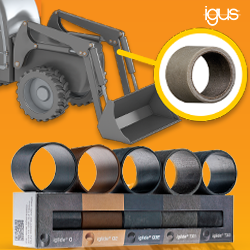
igus® - triflex® R robot dresspacks
Properly managed cables on a multi-axis robot are the difference between successful, failure-free operation and frequent unplanned downtime and lost profits. Discover how triflex® robot dresspacks are designed to protect cables in multi-axis motion - extending cable life, minimizing costs, and reducing unplanned downtime.