Liquid Robotics and Boeing Demonstrated Groundbreaking Autonomous Maritime Warfare Capabilities at the British Royal Navy's Unmanned Warrior Demonstration
Unmanned Surface Vehicles autonomously detected and tracked a live submarine
SUNNYVALE, CA, October 31, 2016 - Liquid Robotics®, the leader in long-duration, unmanned surface vehicles (USVs), and Boeing have for the first time used a network of persistent USVs to detect, report and track a live submarine in a naval demonstration.
Four Sensor Hosting Autonomous Remote Craft (SHARCs) were deployed off the coast of Northern Scotland during the British Royal Navys Unmanned Warrior 2016 demonstration. The autonomous surface vehicles used advanced Boeing acoustic sensors in the live anti-submarine warfare (ASW) mission.
Over the two-week demonstration, the SHARCs successfully detected and tracked an advancing unmanned underwater vehicle and most significantly—a manned diesel submarine. The SHARCs provided detailed and actionable intelligence to commanders through more than 100 automated contact reports, proving the USVs efficacy to autonomously conduct ASW missions and exchange data in real time.
"The Boeing and Liquid Robotics team are redefining the state of the art for autonomous maritime warfare," said Kory Mathews, Vice President, Autonomous Systems for Boeing Defense, Space & Security. "Our work during Unmanned Warrior demonstrates without a doubt the practicality of using autonomous systems to provide real-time actionable intelligence to our warfighters."
In addition to the ASW mission, two SHARCs equipped with meteorological and oceanographic sensors were deployed to the North Atlantic to gather data that ultimately contributed to sensor prediction models for Unmanned Warrior and Joint Warrior, a major bi-annual collective training exercise also hosted by the Royal Navy. The SHARCs operated 24/7 in harsh conditions unfavorable for manned operations - waves in excess of 6.6 meters and winds of more than 60 knots - to autonomously provide real-time data on the weather and ocean conditions critical to the safe operation of the Unmanned Warrior systems.
"Together, Liquid Robotics and Boeing achieved a groundbreaking milestone in unmanned maritime warfare," said Gary Gysin, President & Chief Executive Officer, Liquid Robotics. "We proved that SHARCs can augment the tedious and dangerous task of continuous maritime surveillance by our warfighters and provide critical real-time intelligence to commanders."
####
About Liquid Robotics:
Liquid Robotics designs and manufactures the SHARC (Sensor Hosting Autonomous Remote Craft) Wave Glider platform. The Wave Glider and SHARC are wave and solar-powered unmanned surface vehicles. With our partners we address many of the planets greatest challenges, by transforming how to assess, monitor, and protect the ocean. We solve critical problems for defense, commercial, and science customers. Visit http://www.liquid-robotics.com to learn more.
Liquid Robotics, SHARC, and Wave Glider are registered trademarks of Liquid Robotics, Inc.
For media questions, please contact: Joanne Masters at press@liquid-robotics.com
Featured Product
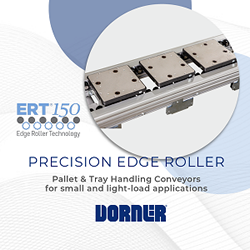
The ERT150 - Dorner's Next Evolution of Edge Roller Technology Conveyors
The next evolution in Dorner's Edge Roller Technology conveyor platform, the ERT®150, is ideal for small and light-load assembly automation, as well as medical and medical-device assembly application. The ERT platform is the only pallet conveyor of its kind available with an ISO Standard Class 4 rating for cleanroom applications. Earning the ISO Standard 14644-1 Class 4 rating means Dorner's ERT150 will conform and not contribute to the contamination of cleanrooms to those standards. As implied by its name, the ERT150 (Edge Roller Technology) uses rollers to move pallets through the conveyor smoothly with no friction (a byproduct often seen in belt-driven platforms). The conveyor's open design eliminates concerns of small parts or screws dropping into rollers and causing conveyor damage or jamming. The ERT150 is suited to operate in cleanroom environments requiring a pallet handling conveyor. It is capable of zoning for no or low-back pressure accumulation and is ideal for automation assembly applications within industries including medical devices, electronics, consumer goods among others.