High performance at low voltage
Tecnotion, the direct drive specialist offers both small iron core and ironless linear motors for low voltage purposes. In addition to 230 Vac and 400 Vac motors for industrial applications, drives are often sought for low-voltage applications of 60Vdc and less.
January 2017, Almelo, The Netherlands - Tecnotion, the direct drive specialist offers both small iron core and ironless linear motors for low voltage purposes. In addition to 230 Vac and 400 Vac motors for industrial applications, drives are often sought for low-voltage applications of 60Vdc and less.
Iron core linear motor with low voltage Z winding
Tecnotions TM3z and TM6z have been customized for use at 48Vac but can be used up to 400Vac. These motors have a special winding to allow traverse speeds of up to 5 m/s at 48Vac, depending on bus voltage. They have the same characteristics as their high voltage siblings:
- A continuous force of 60N to 120N
- Peak force of 105N to 210N
- Low attraction force between the coil unit and magnet plate
- and a very small footprint for applications with little space available.
Ironless linear motors (UC and UF series)
UC and UF series ironless linear motors operate standard at 60Vdc. A total of four motors are available in the UC and UF series. The motors cover continuous forces from 10N to 39N and peak forces between 36N and 85N. Installation dimensions are very small with a 51mm and 53mm width and a maximum of 16mm in height (horizontal mounting). A major advantage of the ironless motors compared to their iron core counterparts, is the absence of cogging, resulting in pinpoint accuracy.
Possible applications are, for example, in medical equipment, robotics, laser engraving machines or in the field of packaging, as well as in applications in which low voltage is required because of operator or customer safety. Due to less restrictive design-standards, the use of low voltage drives can save on design, assembly and commissioning costs.
Featured Product
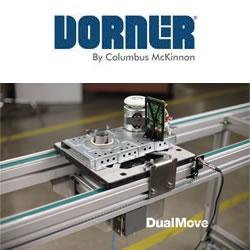