RE2 Robotics Wins Navy Contract to Develop Underwater Manipulator Arms
RE2 Robotics, a leading developer of robotic manipulator arms, announced today that the Company has received a Phase II Small Business Innovation Research (SBIR) award to develop an inflatable Underwater Dual Manipulator system for the US Navys Office of Naval Research (ONR).
PITTSBURGH, PA - February 7, 2017 - RE2 Robotics, a leading developer of robotic manipulator arms, announced today that the Company has received a Phase II Small Business Innovation Research (SBIR) award to develop an inflatable Underwater Dual Manipulator system for the US Navys Office of Naval Research (ONR).
Explosive Ordnance Disposal (EOD) divers are often placed in harms way while performing underwater location and identification of Improvised Explosive Devices (IEDs) on vessels, bridges, and underwater structures such as piers. The integration of a cost-effective and reliable manipulation system onto an Unmanned Underwater Vehicle (UUV) promises to bring the stand-off capabilities that robotic systems have brought to EOD technicians operating on land to those operating underwater.
During Phase I, RE2 engineers designed an inflatable underwater dual manipulation system. This development effort produced a novel design concept for underwater dexterous manipulation that is light-weight, low-cost, and easily deployable in the field as a payload for UUVs. A prototype will be developed and tested during Phase II. Ultimately, the manipulator arms will be used as a collaborative robotic system to assist EOD divers in dismantling IEDs and other hazards.
"Developing robotic technologies that keep individuals out of harms way is paramount to the mission of RE2 Robotics," stated Jorgen Pedersen, president and CEO of RE2. "Historically, we have developed manipulation systems for EOD ground robots. Over the past year we have worked closely with the Navy to transition our expertise to underwater systems. By extending our manipulation capabilities into the submersible space, we are able to enter new markets, such as Offshore Oil and Gas, which rely on the safe inspection, maintenance and repair of underwater structures. Providing dexterous manipulation capabilities to this class of UUVs will open up a new realm of capabilities and applications for unmanned systems."
Featured Product
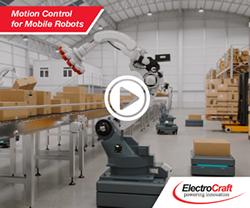