PMAT offers secure global grip in automation
Vacuum tooling system enables smaller, lighter and less expensive automation solutions.
Hingham, MA - Highly versatile and cost-effective, Piab's Modular Automation Tooling system PMAT is available across the globe, helping manufacturers to realize secure, flexible and adjustable vacuum gripper/fixture tools for their assembly lines.
" Our customers particularly appreciate the flexibility of PMAT and the wide range of options offered. They are also very impressed when they realize how easy it is to maintain the system, and the fact that spare parts and qualified service support are readily available globally is definitely one of the most important arguments for choosing PMAT," comments Barry Gropp, District Sales Manager for Piab in Detroit Michigan, where the US automotive industry has favored PMAT for a number of years.
PMAT has enjoyed particular success in automotive body-in-white (BIW) and stamping assembly areas, but is equally applicable to general assembly within any industry. Attachments include vacuum ejector units based on Piab's energy-efficient COAX® technology, providing both grip and release mechanisms.
Following requests from customers, PMAT is offered with an optional inline filter, and an external check-valve that can be used to meter air flow to the unit, protecting it from over pressurization while saving air. The vacuum check valve included in the VGS™3040 platform is an alternative to clamps, saving weight and trapping the vacuum in case of air interruption to the tooling. Furthermore, special suction cup attachments ensure safe handling of objects of varying geometries.
About Piab
Established in 1951, Piab designs innovative vacuum solutions that improve the energy-efficiency, productivity, and working environments of vacuum users around the world. As a reliable partner to many of the world's largest manufacturers, Piab develops and manufactures a complete line of vacuum pumps, vacuum accessories, vacuum conveyors and suction cups for a variety of automated material handling and factory automation processes. Piab utilizes COAX®, a completely new dimension in vacuum technology, in many of its original products and solutions. COAX® cartridges are smaller, more energy efficient and more reliable than conventional ejectors, and can be integrated directly into machinery. This allows for the design of a flexible, modular vacuum system. In 2016, Piab completed two strategically important acquisitions, Kenos and Vaculex. Piab is a worldwide organization with subsidiaries and distributors in almost 70 countries. Its headquarters are in Sweden.
Featured Product
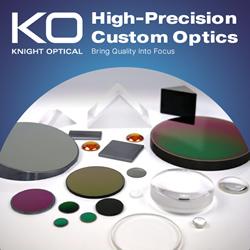
Knight Optical - Unlocking Precision for the Robotics and Automation Revolution
In the era of Industry 4.0, automation and machine learning drive the future. Knight Optical stands at the forefront, collaborating globally to supply precision optical components that power the robotics and automation sector. From UAVs, drones, and robotics to machine vision, LiDAR-driven car sensors, and renewable energy, our optics empower innovation. Optical components play an important role within the industry, including: Optical windows and domes safeguard systems in unmanned vehicles while preserving the field of view for cameras. Infrared lenses with aspheric surfaces elevate thermal imaging. Optical filters excel in machine vision, with colour glass, interference, and dichroic filters in our stock. Knight Optical provides stock components and custom solutions made to your exact specs. With every component undergoing rigorous metrology and QA checks before shipment, you are sure to experience true precision, innovation, and assurance.