New lightweight micro gripper designed for small fragile part assembly
A lightweight micro gripper, the MGR5 was designed for small, fragile part assembly. The MGR brings operation force 10 gram or less capability into range. Light moving mass reduces impact force during small product placement.
New lightweight micro gripper designed for small fragile part assembly
A lightweight micro gripper, the MGR5 was designed for small, fragile part assembly. The MGR brings operation force 10 gram or less capability into range. Light moving mass reduces impact force during small product placement.
MGR5 Specs:
• Compact and lightweight
• Light force capability 10g or less
• Soft-Land capability for pick and place of delicate and fragile parts
• Each jaw can be independently controlled in force, position and velocity
• 5 micron linear encoder standard, 1 micron optional
SMAC electric grippers incorporate programmable speeds, positions and forces with data feedback. The ability to independently control each jaw allows precise force control, measurement and positioning. This makes them ideal for a wide range of positioning, measuring, and inspection applications, particularly where 100% verification is required.
Click on the following link to view a YouTube video on the MGR5: https://youtu.be/xFKf8cvsI3s?list=PLrKivfJ0mSQmipxBvNOFax0cXtwT0s5iZ
Click on the link below to view more information on the MGR5 Micro Gripper from SMAC: https://www.electromate.com/assets/catalog-library/pdfs/SMAC/SMAC%20MGR5-010-5X-1_B_LAH-PT26-26%20Spec_Sheet.pdf
For more information, please contact:
EDITORIAL CONTACT:
Warren Osak
sales@electromate.com
Toll Free Phone: 877-737-8698
www.electromate.com
Tags: SMAC, MGR5, Micro Gripper, Electromate
Featured Product
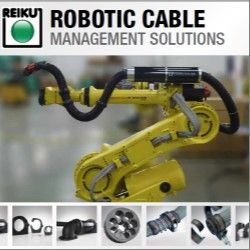
REIKU's Cable Saver™ - The Most Versatile Modular Robotic Cable Management Solution
REIKU's Cable Saver™ Solution eliminates downtime, loss of revenue, expensive cable and hose replacement costs, maintenance labor costs. It's available in three sizes 36, 52 and 70 mm.
All of the robots cables and hoses are protected when routed through the Cable Saver™ corrugated tubing.The Cable Saver™ uses a spring retraction system housed inside the Energy Tube™ to keep this service loop out of harms way in safe location at the rear of the Robot when not required. The Cable Saver™ is a COMPLETE solution for any make or model of robot. It installs quickly-on either side of the robot and has been tested to resist over 15 million repetitive cycles.
REIKU is committed to providing the most modular, effective options for ensuring your robotic components operate without downtime due to cable management.
www.CableSaver.com