Yaskawa Motoman MPX3500 Robot Creates Consistent Finish in Coating Applications
The fast, six-axis MPX3500 robot offers superior performance and efficiently creates a smooth, consistent finish in painting and coating applications. It offers a flexible, compact design and is ideal for painting parts of nearly any size and shape, including recessed, curved or contoured surfaces.
The fast, six-axis MPX3500 robot offers superior performance and efficiently creates a smooth, consistent finish in painting and coating applications. It offers a flexible, compact design and is ideal for painting parts of nearly any size and shape, including recessed, curved or contoured surfaces.
The MPX3500 has a 15 kg wrist payload capacity and a 25 kg upper arm payload capacity, enabling spray equipment to be mounted directly on the robot arm. It also features a 2,700 mm horizontal reach and ±0.15 mm repeatability.
The MPX3500 features a hollow wrist with a large inside diameter of 70 mm which accommodates the mounting of spray equipment applicators with large hose bundles. Interference between the hoses and parts/fixtures is avoided, ensuring optimum cycle time, robot reach and part access.
The robots L-axis is designed with no offset - enabling installation of the manipulator close to a workpiece and higher density robot spacing - saving valuable floorspace. It can be floor-, wall- or ceiling-mounted to provide layout flexibility.
The MPX3500 robot and DX200-FM controller feature Factory Mutual (FM) approval for use in Class I, Div. 1 hazardous environments. An intrinsically safe pendant is available as an option.
The DX200-FM controller includes application-specific software for paint applications and coordinates operation of the robot and painting devices, including spray gun, color changer and gear pump. The controller supports standard networks (EtherNet, EtherNet IP, CC-Link, DeviceNet, EtherCAT and PROFINET), enabling connection to paint equipment controllers and production line controllers.
The DX200-FM is available with Category 3 Performance Level d (PLd) Functional Safety Unit (FSU), which supports safety-rated speed control, safety-rated soft axis and space limiting, and safety-rated monitor stop. In addition to enabling safe operation in shorter and narrower spray booths with adjacent manual operations, these safety functions can be utilized to save costs and reduce floorspace requirements.
About Yaskawa Motoman
Founded in 1989, the Motoman Robotics Division of Yaskawa America, Inc. is a leading robotics company in the Americas. With over 360,000 Motoman® robots installed globally, Yaskawa provides automation products and solutions for virtually every industry and robotic application; including arc welding, assembly, coating, dispensing, material handling, material cutting, material removal, packaging, palletizing and spot welding. For more information please visit our website at www.motoman.com or call 937.847.6200.
Featured Product
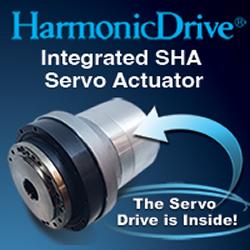