Automated painting solution for general industry
Dürr and Kuka introduce jointly developed robot system for the US market
Southfield, Mich., June 20, 2017 - Dürr and Kuka, leading manufacturers in the fields of production and automation technology, have joined forces: together they have developed an integrated solution for automated paint application in the form of a compact robot for general industry.
While the robot comes from Kuka, Dürr provides the paint application technology. Pre-installed and ready-to-spray, the robot contains fully compatible, tried-and-tested components and offers a unique combination in the market. It is perfectly suited for the requirements of general industry. Areas of application include the painting of wood, plastics, glass and metal. The robot will be introduced to the US market at the AWFS Trade Show in Las Vegas this July and at the FABTECH Trade Show in Chicago in November.
Dr. Hans Schumacher, Board Spokesman of Dürr Systems AG, says: "General industry has seen a growing need for a fully automated paint application of the highest quality. The new painting robot system offers a perfect complement to Dürr's product portfolio in the form of a compact painting robot for customers in general industry. The new solution is a true innovation in this market segment."
The painting robot system consists of a small six-axis robot equipped with state-of-the-art paint application technology. This technology is available in different configurations, tailored to each individual customer project. The system, with all its different components, is completed and pre-commissioned at Dürr. It is thus ready to use ("ready2spray"), can be quickly installed at the customer's site, and ensures efficient processes and a consistently high-quality paint finish.
The ready2spray robot enables the application of solvent- and water-based one- and two-component paints. It can be equipped with matching dosing pumps, paint pressure regulators and color changers. Depending on the requirements, it comes with automated spray guns (air-atomizing or airless) from the EcoGun range or with electrostatic high-speed rotating atomizers from the EcoBell range, both by Dürr.
Dürr is the world leader in automotive painting and car body sealing through its painting and sealing robots as well as its application technology. As in the automotive industry, Dürr also covers the entire spectrum of paint application in the industrial sector. Customers receive all components from a single source. These include the four product categories of pump and fluid-handling equipment, conventional application technology (spray guns), two-component systems as well as solutions for electrostatic application.
With its small dimensions and pre-installed application technology, the ready2spray solution in the form of the compact industrial robot is an innovation in industrial painting. Its integrated concept includes the motion control of the robot and the process control for the applications, housed together in one control cabinet. Furthermore, the new painting system is fully Industry 4.0-ready.
"Dürr also offers a large version for general industry using its own painting robots, which have been tried-and-tested in the automotive industry. This is an automated system for painting larger workpieces. We can thus cover the entire range of customer requirements", says Dr. Schumacher.
Dürr has been sourcing industrial robots from Kuka for a number of years and equipping these with its own application and robot technology for sealing and gluing in automotive production. For paint applications in the automotive industry, Dürr will continue to exclusively offer robots developed and produced in-house. Kuka does not operate in this field.
About the Dürr Group
The Dürr Group is one of the world's leading mechanical and plant engineering firms with outstanding automation expertise. Products, systems and services offered by the Group enable highly efficient manufacturing processes in different industries. Dürr supplies sectors like the automotive industry, the mechanical engineering, chemical and pharmaceutical industries, and the woodworking industry. The company has 86 business locations in 28 countries. The Group generated sales of € 3.57 billion in 2016. Dürr has around 14,400 employees and operates in the market with five divisions:
• Paint and Final Assembly Systems: paint shops and final assembly systems for the automotive industry
• Application Technology: robot technologies for the automated application of paint, sealants and adhesives
• Measuring and Process Systems: balancing equipment as well as assembly, testing and filling technology
• Clean Technology Systems: exhaust-air purification systems and energy efficiency technology
• Woodworking Machinery and Systems: machinery and equipment for the woodworking industry
The Dürr Group has been established in the United States since 1970 and currently employs around 880 people. From the new Campus with a state-of-art validation, testing, and training center in Southfield, MI, Dürr USA represents four of the five divisions. Paint and Final Assembly Systems offers equipment for painting and assembly processes, while Application Technology provides paint application systems. Dürrs Clean Technology Systems is the global leader in air pollution abatement and energy efficient technologies. The subsidiary Schenck Trebel Corporation, based in Deer Park, New York, offers balancing machines, vibration and condition monitoring systems and services for the general industry. The customers of Dürr USA include automotive and commercial vehicle manufacturers as well as their suppliers, and a diverse group of other industries. HOMAG Machinery North America operates the production facilities for HOMAG Group in Grand Rapids, MI, which is also the base for sales and service company Stiles Machinery Inc.
Featured Product
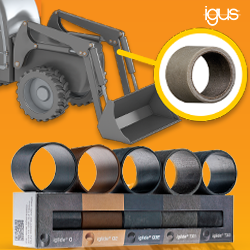
igus® - Free heavy-duty plastic bearings sample box
The iglide® heavy-duty sample box provides a selection of five unique iglide bearings, each suitable for use in heavy-duty equipment due to their self-lubricating, dirt-resistant properties. Each bearing material boasts unique benefits and is best suited for different application conditions, though each can withstand surface pressures of at least 11,603 psi at 68°F.