Autoliv Deploys Lean Execution System Globally
Leading2Lean's Lean Execution System Now Deployed in All Autoliv Manufacturing Plants Across the Globe Cloud-based system allows Autoliv to have a seamless view of real time data across multiple plants, and multiple systems, in 27 countries
August 23, 2017 - Salt Lake City, Utah - Leading2Lean announced today that the company's Lean Execution System (LES) has been fully rolled out across Autoliv's 82 facilities in 27 countries. Autoliv (NYSE: ALV and SSE:
"Autoliv has been our customer for many years and we are thrilled that our LES is now being used across their many plants and facilities," said Keith Barr, CEO of Leading2Lean. "Autoliv started using our LES in just a few plants. Once they saw how our solution improved plant efficiency, plant production and employee morale, they decided to do a global rollout. We look forward to working with Autoliv for many years to come."
Leading2Lean's Lean Execution System is cloud-based and works across existing legacy systems, tying operations together and providing full-plant insights and analysis. Because the system is cloud-based, it is low cost, low risk and high reward. The LES helps manufacturers obtain true lean performance by focusing on problems and problem resolution in real time.
Problems on the plant floor are quickly identified, resources to fix problems are quickly dispatched, down time and waste are reduced, and efficiency improves.
The partnership between Leading2Lean and Autoliv began five years ago with the implementation of LES in several plants. The success of the LES in those plants led company executives to deploy the system across the entire Autoliv plant and facility network. The cloud-based technology enabled better communication and sharing of ideas across the network.
"A focus on quality is our top priority, and we've found a global partner in meeting this objective with Leading2Lean," said Phil Anderson of Autoliv.
"We have seen faster response to problems, more accountability and greater efficiency across our plant network."
Since the global rollout of Leading2Lean's Lean Execution System, key results for Autoliv have included:
- 30% improvement in response time to maintenance issues
- 5% improvement in operational availability
- 12% reduction in cost of spare parts
- Significant reduction in cost of product
- Improvements in other areas such as Preventative Maintenance (PM) completion, Overall Equipment Effectiveness (OEE), Mean Time to Repair (MTTR), and response time to quality issues
- Overall job satisfaction and improved employee performance.
About Leading2Lean
Founded in 2010, Northern Nevada-based Leading2Lean is focused on solutions for multinational manufacturers. Leading2Lean is focused on operational excellence and run by an executive team with extensive experience in manufacturing, engineering, and turning around failed enterprises. Its cloud-based systems provide critical real-time information to help rank-and-file workers do their jobs better and take ownership of their work.
A better-focused and motivated workforce produces more and of better quality, and leads to habits of continuous improvement. For more information, visit leading2lean.com.
About Autoliv
Autoliv, Inc., the worldwide leader in automotive safety systems, develops and manufactures automotive safety systems for all major automotive manufacturers in the world. Together with its joint ventures, Autoliv has more than 80 facilities and 70,000 employees in 27 countries. In addition, the Company has 22 technical centers in ten countries around the world, with
19 test tracks, more than any other automotive safety supplier. Sales in
2016 amounted to about US $10.1 billion. The Company's shares are listed on the NewYork Stock Exchange (NYSE: ALV) and its Swedish Depository Receipts on the Nasdaq Stockholm (ALIV sdb). For more information about Autoliv, please visit our company website at www.autoliv.com.
Featured Product
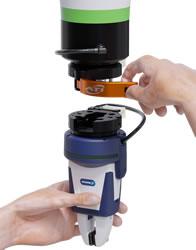
ATI Industrial Automation - MC-50 Manual Tool Changer
With intuitive and ergonomic lever operation, the patent-pending MC-50 Manual Robot Tool Changer provides a simple solution for quickly changing robotic end-of-arm tooling by hand. This compact and robust Tool Changer is designed for applications on collaborative robots that support payloads up to 25 kg and small industrial robots supporting payloads up to 10 kg. Featuring an ISO 50 mm mounting interface on the Master-side and Tool-side, the low-profile MC-50 mounts directly to most cobots and seamlessly integrates with many common cobot marketplace grippers and end-effectors.