New Compact Inductive Linear Position Sensor from Balluff
Continuous Feedback for Grippers & Clamps
Balluff announces the release of the new BIP04 Compact Inductive Linear Position Sensor. The BIP04 provides accurate, continuous linear position feedback over a 17 mm range, in an extremely compact form factor. The BIP04 is ideal for position feedback on machine tool clamping spindles, pneumatic grippers, and any other application requiring linear position feedback in a confined space.
The BIP04 compact inductive linear position sensor is available in analog 0-10V, analog 4-20 mA, and IO-Link interface versions. In addition, the BIP04 offers the following features:
Non-contact inductive technology ensures dependable operation and long service life.
Field-teachable measuring range offers maximum flexibility and customization possibilities.
Fully potted housing provides protection against damage in harsh machine environments.
About Balluff Inc.: Balluff Inc., the U.S. subsidiary of Balluff GmbH, Neuhausen, Germany, is a leading manufacturer of a wide range of inductive, photoelectric, vision, capacitive and magnetic sensors as well as linear position transducers, RFID systems, and networking products. Balluff products for OEM and factory floor solutions are used to control, regulate, automate, assemble, position, and monitor manufacturing, assembly, and packaging sequences for industries including: metalworking, automotive, plastics, material handling, wood processing, aerospace, alternative energy, medical, electrical, and electronics.
Featured Product
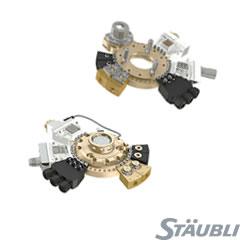
Stäubli robotic tool changer solutions
Stäubli is a pioneer in the construction and development of robotic tool changing systems. Our customers benefit from our many years of expertise in all industry sectors, as well as our modular product concept, which offers three efficient solution paths: MPS COMPLETE offers preconfigured robotic tool changers for immediate use. MPS MODULAR allows the user to determine the configuration, while MPS CUSTOMIZED allows the construction of special, application-specific systems.