CANopen Brushless Servo Amplifiers establish a new benchmark in versatility
The DigiFlex® Performance™ panel and pcb mount servo drives offer full tuning control of all servo loops and are designed for distributed or centralized servo systems. These servo drives utilize CANopen® communication and are commissioned with AMC's user friendly DriveWare® Software via an RS-232 interface.
CANopen is a robust and low cost serial protocol that offers enhanced diagnostic and control capabilities with reasonable bandwidth. Advanced Motion Controls DigiFlex® Performance™ drives follow the CiA DS301 communications profile and the CiA DS402 device profile.
The DigiFlex® Performance™ panel and pcb mount servo drives offer full tuning control of all servo loops and are designed for distributed or centralized servo systems. These servo drives utilize CANopen® communication and are commissioned with AMCs user friendly DriveWare® Software via an RS-232 interface.
AMCs CANopen DigiFlex® Performance™ drives features:
• Standardized object set and device profiles specific to motion control
• Centralized control reduces bus traffic
• 1M bit/sec max speed
• 130 ms message time
• Close to 1 kHz servo drive update rate possible
• Readily available 3rd party peripheral hardware for different platforms
CLICK BELOW for more information on the CANopen servo amplifiers from Advanced Motion Controls.
https://www.servo2go.com/search.php?search=DPCANTE&D=PROD
For more information, please contact:
EDITORIAL CONTACT:
Warren Osak
warren@servo2go.com
Toll Free Phone: 877-378-0240
Toll Free Fax: 877-378-0249
www.servo2go.com
Tags: Advanced Motion Controls, DigiFlex® Performance, Servo Amplifier, Servo Drive, Servo2Go, CANopen, PWM Drive
Featured Product
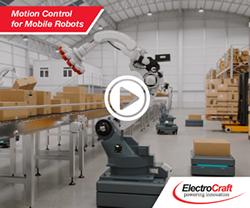