Velodyne Demonstrates Quantum Leap in LiDAR Technology
The new VLS-128™ sensor changes the game for all autonomous driving programs by delivering LiDAR with unprecedented performance for superior real-time perception
SAN JOSE, Calif.--(BUSINESS WIRE)--Under the leadership of visionary inventor and entrepreneur David Hall, Velodyne LiDAR - the world leader in 3D vision systems for autonomous vehicles - today announced its new VLS-128™ LiDAR sensor for the rapidly expanding autonomous vehicle market. Featuring an industry-leading 128 laser channels, the VLS-128 is an extreme step forward in LiDAR vision systems, featuring the trifecta of highest resolution, longest range, and the widest surround field-of-view of any LiDAR system available today.
"With Velodynes efforts in advanced robotics, my goal is to reinvent manufacturing in the United States, making the business case for US-based production that gets shipped to autonomous vehicle development projects the world over"
Tweet this
"The VLS-128 is the best LiDAR sensor on the planet, delivering the most advanced real-time 3D vision for safe driving," said Mike Jellen, President, Velodyne LiDAR. "Automotive OEMs and new tech entrants in the autonomous space have been hoping and waiting for this breakthrough."
Velodynes VLS-128 succeeds the HDL-64, still considered to be the industry benchmark for high resolution. Velodynes new flagship model has a whopping 10 times higher resolving power than the HDL-64, allowing it to see objects more clearly, while its highly accurate object identification and detection system can provide superior collision avoidance in a moving car. The ultra-high resolution of the VLS-128 provides the most advanced safety capabilities on the market for cars driving at all speeds and especially at highway speeds when decisions are made in a split second.
"The Velodyne VLS-128 is an all-out assault on high-performance LiDAR for autonomous vehicles. With this product, we are redefining the limits of LiDAR and we will be able to see things no one has ever been able to see with this technology," said David Hall, Founder and CEO, Velodyne LiDAR. For more insights from Hall on the inspiration behind this new product and how itll impact the autonomous vehicle industry, read here.
Velodyne has performed customer demonstrations of the VLS-128 and plans to produce it in scale at the companys new Megafactory in San Jose. Hall adds, "We have been demonstrating the product for the first time to customers and they cant wait to get their hands on them. We will be shipping the VLS-128 by the end of 2017."
"With Velodynes efforts in advanced robotics, my goal is to reinvent manufacturing in the United States, making the business case for US-based production that gets shipped to autonomous vehicle development projects the world over," said Hall.
The VLS-128 technology provides three major advances for autonomous driving: A reduction in vision system compute complexity, highway driving, and robotic assembly of the sensor itself.
The VLS-128s high-resolution data can also be used directly for object detection without additional sensor fusion, which improves the safety and redundancy of the autonomous vehicles compute function and reduces overall compute complexity.
With its long range and high-resolution data, the VLS-128 allows autonomous vehicles to function equally as well in highway scenarios and low-speed urban environments. It is designed to solve for all corner cases needed for full autonomy in highway scenarios, allowing for expanded functionality and increased testing in new environments.
Based on mass-produced semiconductor technologies, the VLS-128 is designed for automated assembly in Velodynes Megafactory using a proprietary laser alignment and manufacturing system to meet the growing global demand for LiDAR-based vision systems.
"The VLS-128 represents all of Velodynes learning from having built and deployed LiDAR sensors around the world for more than a decade," said Anand Gopalan, Chief Technology Officer, Velodyne LiDAR. "The result is the highest performing LiDAR sensor on the market when considering the combination of field-of-view, range, resolution, and reducing computational burdens of the perception system."
Velodyne LiDAR invented and patented the worlds first 3D real-time LiDAR sensor for autonomous vehicles. Over the last ten years, Velodyne sensors have been installed in thousands of vehicles around the world, traveling millions of real-world miles. Velodyne is the industry standard for localization and environmental perception, providing the core technology for dozens of autonomous vehicle programs in over 10 countries.
About Velodyne LiDAR
Founded in 1983 and headquartered in Silicon Valley, Velodyne is a technology company known worldwide for its real-time 3D LiDAR computing and software platforms. The company evolved after founder/inventor David Hall developed the HDL-64 Solid-State Hybrid LiDAR sensor in 2005. Since then, Velodyne LiDAR Inc. emerged as the unmatched market leader of real-time 3D vision systems used in a variety of commercial applications including autonomous vehicles, vehicle safety systems, mobile mapping, aerial mapping, and security. Its products range from the high-performance, surround view Ultra-Puck™ VLP-32, classic HDL-32/64 and cost-effective VLP-16, to the upcoming, hidden Velarray™. Velodynes rich suite of perception software and algorithms are the key enablers of its perception systems. Velodyne supports customers from offices in San Jose, Detroit, Frankfurt, and Beijing. For more information, visit http://www.velodynelidar.com.
Featured Product
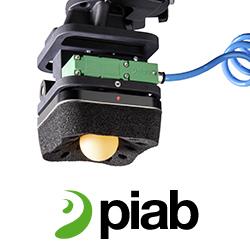