How does OCTOPUZ change your CAD models into functional components in the virtual world? Register for our webinar!
OCTOPUZ is hosting a webinar of approximately 30 minutes where they will show you how they import the CAD geometry of a cell and apply kinematics to particular components in order to make them fully functional for the implementation process.
Every robot cell is different. Some have rails others have positioners or conveyors. Within OCTOPUZ you can create your cell in the virtual world in order to simulate and test your program prior to posting your code to the robot.
Within OCTOPUZ you can match the virtual world with the real world, including the exact external axes and robots that YOU use. Although OCTOPUZ has an extensive library of components, there are times in which we don't have the exact same component as the one in your cell, so what do we do?
In a typical implementation process for a new customer the OCTOPUZ team takes the CAD model of your components and applies the appropriate kinematics to these solids to make them functional . This allows the component to interact and move within the simulation world and results in a fully functional robot cell. Pretty amazing!
In this webinar of approximately 30 minutes we will show you how we import the CAD geometry of your cell and apply kinematics to particular components in order to make them fully functional for the implementation process.
This webinar will cover the following topics:
• Cell Creation
• CAD Import
• Modeling - Component Building
• Kinematics
• Simulation
• Customer Implementation
For more information and to register for this webinar, visit our website!
Featured Product
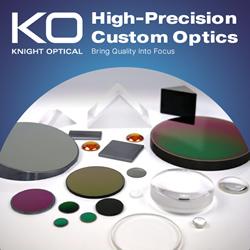
Knight Optical - Unlocking Precision for the Robotics and Automation Revolution
In the era of Industry 4.0, automation and machine learning drive the future. Knight Optical stands at the forefront, collaborating globally to supply precision optical components that power the robotics and automation sector. From UAVs, drones, and robotics to machine vision, LiDAR-driven car sensors, and renewable energy, our optics empower innovation. Optical components play an important role within the industry, including: Optical windows and domes safeguard systems in unmanned vehicles while preserving the field of view for cameras. Infrared lenses with aspheric surfaces elevate thermal imaging. Optical filters excel in machine vision, with colour glass, interference, and dichroic filters in our stock. Knight Optical provides stock components and custom solutions made to your exact specs. With every component undergoing rigorous metrology and QA checks before shipment, you are sure to experience true precision, innovation, and assurance.