ServoStep Integrated Stepper Motor in size NEMA 17, torque up to 0.8 Nm
The new ServoStep integrated stepper motor series MIS171 to MIS176 have a NEMA 17 42x42 mm flange and include controller with 6 different industrial Ethernet protocols, absolute multiturn encoder, closed loop and M12 connectors.
Birkerød, Denmark - JVL Industri Elektronik A/S, one of the world leaders in the field of integrated servo - and stepper motors introduce a new compact and slim stepper motor. The new ServoStep integrated stepper motor series MIS171 to MIS176 have a NEMA 17 42x42 mm flange and include controller with 6 different industrial Ethernet protocols, absolute multiturn encoder, closed loop and M12 connectors. This new motor family is based on the latest microprocessor and cooling technology and an advancement compared to previous designs.
All the necessary electronics in a stepper system are integrated in the motor itself and are similar to the concept used by other JVL motors, making it very easy to use in all kind of motion control stepper or servomotor applications. The motor contains everything needed to solve a modern control task, either as a stand-alone with own easy programmable motion controller or controlled from an external PLC or PC. 8 I/O points can be individually configured as digital input, digital output or analogue input. Modbus RTU or CANopen provide easy connections to a PLC or HMI. An ActiveX/OCX driver is available to make simple interface to LabView, Excel, VB or other Windows-programs. Up to 254 axis can be connected on the same RS485 bus.
Key features:
• Industrial Ethernet. 6 Protocols
• Very high motor power and torque
• Closed-loop operation with current control
• Absolute multiturn encoder
• Safe Torque Off (STO) input
• High resolution 409600 cnt/rev.
• Speed 0-3000 in 0.01RPM steps
• Wide supply range 7-72 VDC
• Protection class up to IP67
• M12 or M23 connectors
Industrial Ethernet:
Profinet, EtherCAT, Powerlink, EtherNet/IP, Modbus TCP or SERCOS III are available and for EtherCAT and SERCOS III synchronization and drive profiles are available. MACtalk can use Ethernet for commissioning the motor so no need for RS232/RS485 converter or additional cables. The motor has the ability to be upgraded with other protocols or newer versions of the same protocol at any time. Because of the upgradeability, the JVL Industrial Ethernet module is also ‘future proof' as newer versions of the protocols will always fit into the design. The motor is equipped with two Ethernet connectors and a built-in switch, enabling line topology without any extra expensive hardware. Several LEDs, enabling technicians and operators to get a quick status overview.
Motor range:
• MIS171 with 0,15 Nm, length 70,5 mm. 5mm shaft
• MIS173 with 0,26 Nm, length 83,5 mm. 5 or 6,35mm shaft
• MIS176 with 0,80 Nm, length 104,3 mm. 8 mm shaft
The motors can be operated as stand-alone units or controlled from a PLC or PC. The 8 I/Os can be individually configured as digital input, digital output or analog input. As standard, it is possible to communicate with holistic systems via for example Modbus RTU or CANopen. The MAC motor standard protocol that is also supported makes it possible to connect up to 254 other JVL integrated motors. The MIS17 series allows connectivity to all industrial Ethernet interfaces such as Profinet, EtherCAT, Powerlink, EtherNet/IP, Modbus TCP and SERCOS III.
Interface:
• Industrial Ethernets Profinet, EtherCAT, Powerlink, EtherNet/IP, Modbus TCP and SERCOS III
• CANopen DSP402 and DS301
• Pulse/Direction mode for electronic gear
• High speed position capture
• ActiveX/OCX driver as well as JVL MacTalk Protocol
• Strong graphic programming with + - * / calculations and advanced features
• SSI interface for external linear or rotary absolute encoders
• External encoder for dual closed-loop.
• RS485 up to 921 kbit and Modbus RTU
• RS422 and RS485 for encoder I/O and connection to external HMI, PLC or encoder
• Point-to-point or multi-axis operation with up to 254 JVL motors on the same RS485 bus
• Wireless Industrial Ethernet through Bluetooth or WLAN
Motor specification:
• Built-in PLC with 8 DIO, 24V or 0-5V (12bit) analog input with advanced filtering
• Speed-precision 0.01 RPM. Acceleration-precision 1 RPM / sec.
• Absolute multi-turn encoder
• Built-in encoder for closed loop and stall detection and control
• Wide supply range of 7-72 VDC provides high torque at high speeds
• Dual supply maintain position values etc. in emergency situations
• Motor current 0-4 Amp RMS and 5,6 Amp peak
• Closed-Loop operation
• Double shaft and brake option
• All connections with M12 connectors in IP67
• Top or rear-end mounted M12 or M23 hybrid connector
Featured Product
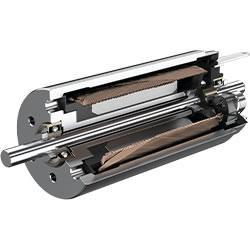