New LCR16 Series Linear Rotary Actuator, 35mm stroke, 24VDC operation with 5 micron encoder
The actuator is constructed with a direct drive brushless servo motor. It's designed with linear guide built-in lubrication to offer long life cycle.
The LCR16 from SMAC Moving Coil Actuators provides precision Z-theta motion within one small actuator, which is ideal for a pick, orient and place applications. A wide variety of LCR16 linear rotary actuators are available with either direct drive or gearbox equipped rotary units.
The vacuum-built-in shaft through the rotary motor is available for some models to prevent dust build-up in the unit. These z-theta actuators can easily be programmed to control force/torque, position and velocity in all axes at the same time with feedback capability. SMAC's unique, patented "Soft-Land" function enables the unit to gently land on a delicate component with a controlled force to avoid damage of both the component and the actuator.
The actuator is constructed with a direct drive brushless servo motor. It's designed with linear guide built-in lubrication to offer long life cycle. Moreover, it provides absolute control over: force/torque, position, acceleration and velocity.
Features include:
• Direct drive brushless servo motor
• Combined linear and rotary motions in a single unit
• Fully programmable in force/torque, position and velocity
• SMAC's Patented ‘Soft-Land' Technology
• Self-lubricated linear guide
• Low shaft run-out, 30µm (Lower run-out optional)
• Vacuum through shaft prevents dust accumulation
• MTBF 100 million life cycle
Information on the LCR16 Series Linear Rotary Actuator from SMAC can be viewed at:
https://www.electromate.com/assets/catalog-library/pdfs/SMAC/SMAC_LCR16_Linear_Rotary_Actuator_Brochure.pdf
Featured Product
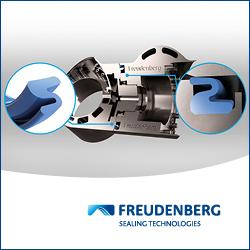
IP Seals for Robots
Freudenberg Sealing Technologies' IPRS (Ingress Protection Seals for Robots) provides reliable protection for robotic systems operating in harsh environments. Designed to prevent dust, moisture, chemicals, and wear from compromising performance, IPRS extends service life and reduces maintenance. The adaptive Z-shaped geometry ensures sealing integrity under continuous motion, making it ideal for high-speed automation and outdoor applications. Manufactured with high-performance elastomers such as Fluoroprene XP and EPDM, IPRS offers exceptional resistance to lubricants, cleaning agents, and extreme temperatures. This makes it the perfect solution for six-axis robots, SCARA robots, AMRs, AGVs, and cobots.
With its low-friction design and durable materials, IPRS enhances energy efficiency and operational reliability in industrial and autonomous robotics. Learn more about our IPRS Seals