Limit Lost Motion with Gam’s New SPH Flange Planetary Gearbox
The compact SPH-F gearbox can be used when space is limited and the ISO 9409 compatible output flange allows for easy mounting of machine elements such as pinions, pulleys, or other adapters.
Greenville, DE — Backlash and Torsional Rigidity are both important values to consider when selecting a high precision gearbox as they both affect lost motion (arcmin). GAM's SPH Flange Gearbox has a single piece steel housing and ring gear machined directly inside for maximum stiffness. The helical gears are precision cut and ground for extremely quiet and smooth torque transmission with a standard backlash rating of < 3 arc-min or < 1 arc-min reduced.
The compact SPH-F gearbox can be used when space is limited and the ISO 9409 compatible output flange allows for easy mounting of machine elements such as pinions, pulleys, or other adapters. To accommodate direct connection to machines, the SPH-F has strong taper roller bearings set at a wide distance and a fully supported planet carrier for high load carrying capacity. The ring gear is machined directly into a single piece steel housing for improved torsional rigidity. Currently offered in three frame sizes, the SPH-F is rated for up to 450Nm nominal and 675Nm acceleration torque in the largest size.
Gam SPH-F Flange Planetary Gearbox features:
• Low Backlash: <3 arcmin standard for single stage units, <1 arcmin reduced backlash
• Smooth and quiet torque transmission
• High load carrying capability
• High torsional rigidity
Download the new SPH brochure to see how the SPH Flange stacks up to other flange gearboxes available on the market when it comes to lost motion.
More information on the GAM SPH Planetary Gearboxes available from Servo2Go.com can be viewed at:
https://www.servo2go.com/catalogsearch/result/index/?product_list_limit=100&q=SPH-F
Featured Product
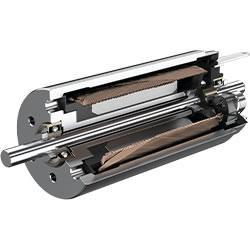