New 20mm Linear Stepper Motor now available from Nippon Pulse
Nippon Pulse is excited to introduce its smallest linear stepper motor yet, the PFL20 Linearstep. The PFL20 is a highly efficient, high thrust tin-can linear actuator with a 20mm diameter and a bipolar winding.
RADFORD, Va. - Nippon Pulse is excited to introduce its smallest linear stepper motor yet, the PFL20 Linearstep. The PFL20 is a highly efficient, high thrust tin-can linear actuator with a 20mm diameter and a bipolar winding.
PFL20 is RoHS-compliant, has a 30/60mm effective stroke, and can reach 6 N of force at 200 pps. With 24 steps per revolution, the lead screw has a 1.2mm thread pitch; the PFL20 also reaches 5V rated voltage, resistance of 33 Ohms/phase and inductance of 12mH/phase. The datasheet with additional specifications can be found here.
The simple structure of Linearstep motors - just a threaded rotor hub and lead screw - helps to save space and reduce costs, due to fewer components needed compared to systems that convert rotary motion to linear. Linearstep motors are also easy to control, and can be ordered with unipolar or bipolar windings and a variety of usable voltages. In addition to the 20mm motor size, this motor is also available in 25mm (captive or non-captive option) and 35mm diameter sizes.
Nippon Pulse's tin-can linear actuators, including the Linearstep, are also available for customization; contact an applications engineer to learn more about our customization capabilities.
Information on the PFL20 from Nippon Pulse can be viewed at:
https://www.electromate.com/assets/catalog-library/pdfs/nippon-pulse/Nippon_Pulse_pfl20_specsheet.pdf
Featured Product
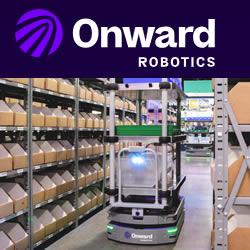
Onward Robotics - Meet Me® Fulfillment Automation
Meet Me uniquely brings talent and technology together: providing end-to-end process efficiency and enabling accurate and continuous fulfillment workflows. Proprietary Pyxis technology uniquely orchestrates picker and Lumabot AMR workflows independently, delivering fast, accurate, and efficient fulfillment from induction to pack out. Learn more about Meet Me Automation: Download Overview Brochure