Optimus Ride Selects Velodyne Lidar’s Trailblazing Sensors to Power its Self-Driving Vehicles
Velodyne Sensors Deliver Industry-Leading Range and Resolution to Optimus Ride Fleet
Velodyne Lidar, Inc. today announced that Optimus Ride will use Velodyne's groundbreaking lidar sensors in its entire fleet of self-driving vehicles. The sensors provide rich computer perception data that enables real-time object and free space detection for safe navigation and reliable operation. Optimus Ride, a leading self-driving vehicle technology company on a mission to transform mobility, will soon be operating its self-driving systems in four U.S. states.
"Velodyne's sensors provide powerful lidar solutions that help us ensure our self-driving vehicles are the smartest and safest on the road today," said Dr. Ryan Chin, Optimus Ride's CEO and co-founder. "For Optimus Ride to operate a fleet at SAE Level 4 requires significant sophistication, intelligence, range and resolution. Velodyne's technology meets these high standards."
Optimus Ride operates self-driving vehicles that provide passenger transportation at low speeds within defined, geofenced areas such as planned communities, campuses and self-driving zones in cities. The company's vehicles are currently deployed in Boston's Seaport District, South Weymouth, Mass. and at the Brooklyn Navy Yard in Brooklyn, New York. Optimus Ride's deployment in the Navy Yard is the first commercial deployment of self-driving vehicles in the state of New York. Optimus Ride will soon deploy at Paradise Valley Estates in Fairfield, Calif. and Brookfield Properties' Halley Rise development in Reston, Va.
Using Velodyne sensors, Optimus Ride can precisely locate the position of people and objects around its vehicles, as well as calculate their speed and trajectory. With that information, the vehicle's on-board computer system determines how to drive to its destination.
"The Optimus Ride fleet showcases how Velodyne's intelligent lidar sensors are helping companies place autonomous vehicles on the road today," said Mike Jellen, President and CCO, Velodyne Lidar. "Optimus Ride has an ingenious approach to providing people with access to efficient and convenient self-driving mobility - effectively solving the first-and last-mile problem."
About Velodyne Lidar
Velodyne provides smart, powerful lidar solutions for autonomy and driver assistance. Headquartered in San Jose, Calif., Velodyne is known worldwide for its portfolio of breakthrough lidar sensor technologies. Velodyne's Founder and CEO, David Hall, invented real-time surround view lidar systems in 2005 as part of Velodyne Acoustics. Mr. Hall's invention revolutionized perception and autonomy for automotive, new mobility, mapping, robotics and security. Velodyne's high-performance product line includes a broad range of sensing solutions, including the cost-effective Puck™, the versatile Ultra Puck™, the autonomy-advancing Alpha Puck™, the ADAS-optimized Velarray™ and the groundbreaking software for driver assistance, Vella™.
About Optimus Ride
Optimus Ride is a self-driving vehicle technology company on a mission to transform mobility. The company develops self-driving vehicle algorithms, software, hardware, and system integration for mobility on demand solutions. Optimus Ride's fully autonomous vehicles are ideal for industrial and office parks, military and academic campuses, smart cities, ports, airports, mixed-use private developments and other geofenced areas. Currently, the self-driving vehicle technology company is deploying Level 4 self-driving systems in cities and campuses in Massachusetts, Virginia, California and New York. With roots at MIT, Optimus Ride's team of outstanding industry experts work closely with the company's clients to design networks and systems specifically for each environment, ensuring end-users reap all of the benefits this technology has to offer. To learn more about how Optimus Ride is bringing the promise and benefits of autonomous vehicles to the real world, visit www.optimusride.com.
Featured Product
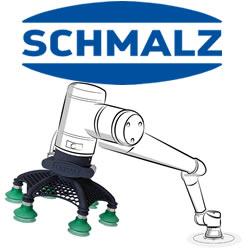
Schmalz Technology Development - The Right Gripper for Every Task
In order to interact with their environment and perform the tasks, lightweight robots, like all industrial robots, depend on tools - and in many cases these are vacuum grippers. These form the interface to the workpiece and are therefore a decisive part of the overall system. With their help, the robots can pick up, move, position, process, sort, stack and deposit a wide variety of goods and components. Vacuum gripping systems allow particularly gentle handling of workpieces, a compact and space-saving system design and gripping from above. Precisely because the object does not have to be gripped, the vacuum suction cupenables gapless positioning next to each other.