Quest Powers Up Its Robotic Pouch Packer and Space-Saving Skid-Based Palletizer at Pack Expo 2019
Quest highlights their Quik Pick & Pack robotic pick and place cell, along with its Boxed-Bot robotic palletizer. Quest Booth #C-3026
Quest Industrial, one of ProMach's newest product brands and key acquisitions, is exhibiting September 23-25 at Pack Expo 2019 in the Las Vegas Convention, where they plan to highlight their Quik Pick & Pack robotic pick and place cell, along with its Boxed-Bot robotic palletizer. Quest Booth #C-3026
Quest is an award-winning, FANUC Authorized system integrator and certified vision specialist, and its systems are capable of direct food contact with U.S. Department of Agriculture compliant and washdown designs. The diverse knowledge base of Quest engineers and programmers encompasses the entire manufacturing process, allowing them to solve virtually any customer application with the appropriate level of robotic automation.
Quest Quik Pick & Pack
The Quest Quik Pick & Pack is a high-speed robotic case packer that's quick, accurate and compact. A main differentiator, among other robotic case packers, is its handling and application speed. Loaded with the QPack custom case packing software, the Quik Pick & Pack can be configured to pick up as many as 1,000 pieces per minute.
The Quik Pick & Pack works extremely well with flexible film packaging, thanks to its vision system and optional 3D scanning that quickly detects the pouches' topography and center of gravity to identify the proper high point for picking. While the ideal application is more geared to flexible film packaging, the Quik Pick & Pack performs well with just about any packaging type that comes from a vertical form fill seal or horizontal flow wrapper machine.
Another distinguishing feature of the Quik Pick & Pack is its flexibility in handling a variety of product shapes, weights, and sizes. The machine can pick and place bags weighing only 1 ounce and reach all the way up to 20 pounds. Additionally, end users can create their own pack patterns to accommodate customers' different packaging requirements.
Features and benefits of the Quest Quik Pick & Pack include:
Accepts a wide range of boxes or cases with continuous changeover from size to size
Accepts a wide range of product types, sizes and textures
Custom orientation of product, including: pile stacks, base stacks, random cuts, shingle stack, and 2-3 stack
Quest Boxed-Bot
The Quest Boxed-Box space-saving skid-based robotic palletizer features a footprint starting at just 8'x10'. The Boxed-Bot allows an operator to design and produce exact pallet patterns quickly and easily from bags to boxes and other product types. Creating patterns is accomplished though the QBox custom pallet building software, the most technologically-intuitive operator interface available on the market. The ability to build your own patterns saves time and money by eliminating the need to have a service programmer onsite to perform the task.
The Boxed-Bot features a long-reach Fanuc M-710IC Series robot that provides higher stack patterns, which better maximizes tractor-trailer loading for more efficient shipping.
ProMach Acquisition
In April 2019, ProMach acquired Quest Industrial as a way to strengthen its robotics integration capabilities. The addition of Wisconsin-based Quest expands ProMach's capacity for sophisticated robotics projects, enhances ProMach's robust robotics support, and strengthens its integrated solutions expertise in a wider range of applications.
To see how the Quik Pick & Pack high-speed robotic case packer and the Boxed-Bot robotic palletizer can improve the flexibility of your packaging production lines, visit Quest Industrial in Booth #C-3026 at Pack Expo 2019. For more information online, visit QuestIndustrial.com [QuestIndustrial.com __title__ Quest Website].
About Quest
Quest is a full-service robotic integrator that specializes in automation solutions across food, beverage, plastics, metal, and other industries needing to optimize floor space, expand operations with accuracy and consistency, and improve overall production line flexibility and efficiency. Many of our packaging solutions meet industry-specific requirements with specialized tooling, software, and protective coatings designed for dairy, produce, and other markets. Our unique robotic solutions include applications in pick and place, cup filling, knife cutting, vacuum sealing, case erecting, tray forming, palletizing, vision and verification systems, and much more, including bundling multiple application technologies into a single robotic packaging cell.
About ProMach
ProMach is a family of best-in-class packaging solution brands serving manufacturers of all sizes and geographies in the food, beverage, pharmaceutical, personal care, and household and industrial goods industries. ProMach brands operate across the entire packaging spectrum: filling and capping, flexibles, pharma, product handling, labeling and coding, and end of line. ProMach also provides Performance Services, including integrated solutions, design/build, engineering services, and productivity software to optimize packaging line design and deliver maximum uptime.
ProMach designs, manufactures, integrates, and supports the most sophisticated and advanced packaging solutions in the global marketplace. Its diverse customer base, from Fortune 500 companies to smaller, privately held businesses worldwide, depends on reliable, flexible, technologically advanced equipment and integrated solutions. ProMach is headquartered near Cincinnati, Ohio, with manufacturing facilities and offices throughout the United States, Canada, Mexico, Brazil, Europe, United Arab Emirates, and China. For more information about ProMach, visit http://www.ProMachBuilt.com.
Featured Product
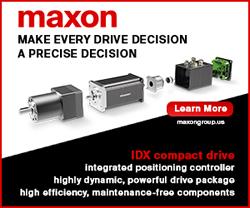
The maxon IDX Compact Drive with Integrated Positioning Controller
The compact brushless EC-i motor combined with an EPOS4 positioning controller delivers a highly dynamic, powerful drive package with field-oriented control (FOC), high efficiency, and maintenance-free components in a high-quality industrial housing. The maxon IDX drives are suitable for use across the entire speed range (from standstill to maximum speed) and have an extremely high overload capability. Together with a positioning controller, the integrated sensor (single turn) enables absolute positioning.