ATI Develops Cobot-Ready Accessory Kits
Complete end-of-arm packages for collaborative robots
Cobot-Ready Accessory Kits from ATI offer users a simple and effective way to increase the flexibility of collaborative robots. ATI's Cobot-Ready Accessory Kits are suited for a wide variety of industries and application types. Tasks such as machine tending, finishing processes, part inspection and analysis, assembly, and many other complex tasks are simple to implement with these all-in-one packages.
The Axia80 Force/Torque Sensor is a high-performance, low-cost sensor that measures all components of force and torque. It offers the highest resolution, accuracy, and stiffness available and gives your cobot the sense of touch to adapt to its environment.
The Axia80 Cobot-Ready Kit includes precalibrated Axia80 sensor, power cables to robot controller, interface plates*, mounting hardware, assembly tool, software files with demo applications. All Axia80 Kit part numbers are specific to robot brand: Universal Robots CB3 series robots (part number: 9105-UR-Axia80), Universal Robots URe series robots (part number: 9105-URE-Axia80), TM Robots (part number: 9105-TM-Axia80). Contact ATI for other robot brand kits.
The Compliant Deburring Blade (CDB) is a motorless deburring tool for operations such as edge deburring, chamfering, countersinking, scraping and deflashing on virtually any material. As the cutting media removes material, the compliance allows for consistent results despite variation in part size, part positioning, or robot location.
The CDB Cobot-Ready Kit (part number: 9150-COB-CDB-01) includes Compliant Deburring Blade tool with axial and radial compliance, Shaviv E100 industrial deburring blade, e-style holder, interface plate*, mounting hardware, assembly tools. CDB Kit also available for Universal Robots UR and URe series robots (part number: 9150-UR-CDB-01).
The QC-11 Automatic Tool Changer is a two-part coupling device that enables a robot to exchange end-of-arm tools automatically. The pneumatically-actuated locking mechanism attaches the tooling to the robot securely without manual intervention.
The QC-11 Cobot-Ready Kit (part number: 9120-COB-011-01) includes QC-11 Tool Changer (Master and Tool sides), electrical modules with 8-pin M8 connectors, lock/unlock sensing kit, cables to robot and to EOAT, interface plate*, mounting hardware, assembly tool. QC-11 Kit available for Universal Robots UR and URe series robots (part number: 9120-UR-011-01). Tool side only Kits with M8 Module and cable to EOAT are also available: (part number: 9120-COB-011T-01. For Universal Robots UR and URe series robots, part number: 9120-UR-011T-01).
The MC-10 Manual Tool Changer is a cost-effective solution for quickly changing tools by hand. The ergonomic twist-collar locking mechanism provides a steadfast connection of the tool to the robot. The MC-10 operates manually and gives tactile feedback that the Tool Changer is locked in place.
The MC-10 Cobot-Ready Kit (part number: 9120-COB-010-01) includes MC-10 Manual Tool Changer (Master and Tool sides), electrical modules with 8-pin M8 connectors, cables to robot and to EOAT, interface plate*, mounting hardware, assembly tool. Tool side only Kit with M8 Module and cable to EOAT is also available: (part number: 9120-COB-010T-01).
*All interface plates are compatible with standard ISO 9409-1-50-4-M6 robot flanges.
Featured Product
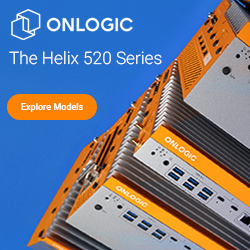
OnLogic's Helix 520 Series of Scalable Fanless Computers
The Helix 520 series utilizes the latest Intel Core Ultra processors with integrated edge AI capabilities to deliver exceptional performance and industrial-grade reliability for demanding applications in automation, robotics, machine vision, and more. Its unique modular design allows for flexible scaling of CPU and GPU performance, while robust connectivity and expansion options ensure seamless integration.