Introducing the IncOder™ Inductive Angle Encoder from Zettlex
Rather than the bulky transformers of traditional inductive sensors, Zettlex sensors use printed circuits. This enables compact, accurate, lightweight and robust position sensors with no contacts, no delicate parts, no maintenance, no hassle – just accurate measurements – all day, every day. IncOders are ideally suited to harsh environments – where potentiometers, optical or capacitive devices may prove unreliable.
Zettlex position sensors (IncOders) use non-contact, inductive technology for precision angle measurement. Rather than the bulky transformers of traditional inductive sensors, Zettlex sensors use printed circuits. This enables compact, accurate, lightweight and robust position sensors with no contacts, no delicate parts, no maintenance, no hassle - just accurate measurements - all day, every day. IncOders are ideally suited to harsh environments - where potentiometers, optical or capacitive devices may prove unreliable.
IncOders have 2 main parts - a Stator and a Rotor - each shaped like a flat ring. The large bore makes it easy to accommodate through-shafts, slip-rings, optical-fibres, pipes or cables. The Stator is powered and the Rotor is passive. The Stator contains the electronics to receive power and generate an output signal. The output signal from the Stator shows the true absolute angular position of the Rotor relative to the Stator without the need of any motion.
IncOder inductive angle encoders do not require compliant or special couplings and the Rotor & Stator can simply be screwed to the host product. Precise mechanical mounting is not required and there are no bearings. Whereas optical or capacitive angle encoders can be unreliable in harsh conditions - notably with condensation or dust - Zettlex angle encoders are generally unaffected by foreign matter and IP67 rated versions are available. Unlike capacitive devices, there is no need to earth the Rotor or Stator. Robust, hard-anodized aluminium alloy housings and monolithic constructions are used throughout. There are no contacting, delicate or wearing parts, so there is no need for periodic replacement, service or mainton Measurement for Extreme Environments
• High-reliability Inductive Angle Encoder Technology
• Simple installation; ‘fit and forget' technology
• Non-contact technology for high reliability in extreme environments
• Proven in Aerospace, Defence, Medical & Industrial applications
• Over 4enance. In other words, IncOder angle encoders are true ‘fit and forget' devices. Features include:
• Robust Angular Positi million product configuration options available
Information on the IncOder™ Inductive Angle Encoder from Zettlex can be viewed at:
https://www.electromate.com/catalog-video-library/zettlex/
Featured Product
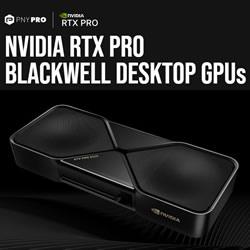