Fetch Robotics Announces Integrated Fulfillment Solution with Zebra Technologies
Combined power of Fetch AMRs and Zebra FulfillmentEdge™ software optimizes picking across multiple orders while dynamically orchestrating workers and robots
MODEX 2020 (Booth #9011) -- Fetch Robotics, the leader in cloud robotics, today announced a collaboration with Zebra Technologies Corporation, an innovator at the edge of the enterprise with solutions and partners that enable businesses to gain a performance edge, to optimize and automate warehouse picking processes through the integration of Fetch Autonomous Mobile Robots (AMRs) and Zebra FulfillmentEdge™ software. The unique solution optimizes picking across multiple orders for piece, case, and pallet workflows. By dynamically optimizing and orchestrating the movement of warehouse workers and robots, FulfillmentEdge and Fetch AMRs enable collaborative picking for faster, more accurate fulfillment and improved workflows that allow workers to spend more time in the aisle instead of manually moving material throughout a facility. The solution will be demonstrated at Fetch's booth (#9011) at MODEX 2020 on March 9-12, 2020 in Atlanta's Georgia World Congress Center.
E-commerce is causing a profound change in supply chain operations that is blurring the line between distribution centers and fulfillment centers as companies increasingly ship to consumers and stores from the same facility. Increasing order volume, labor shortages, high turnover, long ramp up times, and physically taxing material movement related to picking are forcing companies to accomplish more with fewer resources. In response, picking operations need to transform so that companies are able to fulfill more orders with fewer and less experienced workers.
The integration of Zebra FulfillmentEdge and Fetch AMRs provides the solution needed for this transformation. Through the combined solution, workers are collaboratively dispatched in optimized pick paths across multiple orders turning manual material movement into high-value, productive picking time. Worker and AMR movements are orchestrated for picking operations but can also interleave other tasks such as replenishment into the flow to better leverage workers' time in the aisles. In addition, FulfillmentEdge can direct Fetch AMRs to other non-picking operations such as removal of recycling, reverse logistics and restocking of packing stations to maximize robot utilization. The solution also makes it easier to train workers for new workflows, reducing training and onboarding time up to 90 percent.
"By integrating Fetch AMRs with Zebra FulfillmentEdge and the optional enterprise-class HD4000 head-mounted display, we have created a solution for companies to modernize their picking operations without having to upgrade their warehouse management system or make changes to their facilities," said Stefan Nusser, VP of Products at Fetch Robotics. "This combined solution enables companies to increase revenue by directing workers to high-value activity, reduce unproductive material movement and dwell time, and improve efficiency across piece, case, and pallet picking operations."
Zebra FulfillmentEdge uses multiple sources of data, including a customer's warehouse management system (WMS) and other back-end systems as well as contextual and mobile device data to direct and synchronize the best-next-action of multiple workers and Fetch AMRs for collaborative picking assignments across multiple orders using picking strategies that include zone picking and wave picking, among others. The picking process is streamlined with visual cues presented as a simplified graphical and numerical overlay in the HD4000 head-mounted display to provide information including item location, pick total, directional prompts and cues showing pickers where to place the right quantities for each customer order on the Fetch AMR cart.
"Warehouse operations leaders need to synchronize their WMS, worker and workflow optimization solutions and new automation deployments to maximize return on investment and minimize risks to supply chain operations," said Joe White, Senior Vice President of Enterprise Mobile Computing, Zebra Technologies. "Combining Zebra FulfillmentEdge with Fetch's broad portfolio of AMRs empowers our joint customers to modernize their warehousing, distribution and fulfillment operations by optimizing the performance of front-line workers alongside AMRs."
About Fetch Robotics
Fetch Robotics is an award-winning intralogistics automation company headquartered in Silicon Valley. By combining autonomous mobile robotics with the power of the cloud, the Fetch Cloud Robotics Platform provides on-demand automation solutions for material handling and inventory management, with the power to find, track, and move almost anything in any facility. Fetch Robotics' solutions and services are deployed in leading distribution, fulfillment, and manufacturing centers around the world, augmenting workforces to drive increased efficiency and productivity. For more information, please visit www.fetchrobotics.com or follow the company on Twitter @FetchRobotics.
ABOUT ZEBRA
Zebra (NASDAQ: ZBRA) empowers the front line of business in retail/ecommerce, manufacturing, transportation and logistics, healthcare, public sector and other industries to achieve a performance edge. With more than 10,000 partners across 100 countries, we deliver industry-tailored, end-to-end solutions that intelligently connect people, assets and data to help our customers make business-critical decisions. Our market-leading solutions elevate the shopping experience, track and manage inventory as well as improve supply chain efficiency and patient care. In 2019, Zebra ranked #166 on Forbes' list of the World's Best Employers, and the company joined the S&P 500 Index. For more information, visit www.zebra.com or sign up for news alerts. Participate in our Your Edge blog and follow us on LinkedIn, Twitter and Facebook.
Featured Product
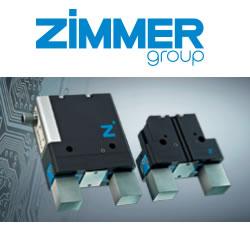