OTTO Motors Helps Sunview Patio Doors Achieve Flexibility, Safety and Efficiency
Faced with customer demand for more customization, Sunview turned to OTTO self-driving vehicles as part of factory modernization
Sunview Patio Doors is better able to meet customer demands while keeping its factory workers safe after implementing OTTO Motors self-driving vehicles to move materials throughout its Ontario manufacturing facility.
A few years ago, Sunview was facing threats from market shifts. Customers were increasingly looking for faster delivery times and customized products. Windows and patio doors were being produced in more varying sizes and materials, and there were now endless options for Sunview to coordinate to keep customers happy. The company, which has been in business for more than 40 years and makes about 80,000 units per year, wanted a leaner manufacturing model to remain competitive. Business leaders needed more flexibility, but they weren't willing to sacrifice efficiency or safety.
"Our customers are smart and know what they want," said Tony Margiotta, president at Sunview. "They know they have options, and it is our job to make sure that we can deliver what they want in order to earn their business."
Sunview first considered Automated Guided Vehicles (AGVs) but realized they weren't a practical option. AGVs require guidance devices such as magnetic tape, beacons or predefined laser paths to travel on fixed paths in controlled spaces. Sunview's factory simply had too many people and moving parts to allow for those. They were worried magnetic tape would get cut or something would block a laser or beacon. Plus, AGVs are less reliable to operate safely around people.
Self-driving vehicles, on the other hand, provide the flexibility, reliability and safety the company needed.
"OTTO filled a niche that I didn't even think was possible," said Kurt Oberparleiter, Sunview's vice president of operations. "The vehicle avoids objects and completes tasks that humans could not. It's just there, the minute you need it. OTTO never hits anything, it doesn't get mad at its coworkers, it doesn't get upset if you put something in front of it, it just does its job."
OTTO uses laser-based perception and artificial intelligence to move through facilities without additional infrastructure. Its onboard sensors and software understand the working environment and adapt to changes in real time. The vehicle detects and avoids people, obstacles and equipment.
"OTTO is the first type of material handling equipment that has a 100% safety rate," said Oberparleiter. "We haven't had a single incident in the year since we installed the self-driving vehicles."
Implementing OTTO was a quick and seamless process, and Sunview was able to reach its ROI in just 16 months. The company is in the process of adding additional OTTO vehicles to the facility.
"At OTTO Motors, we are dedicated to developing innovative products that are powering the future of manufacturing," said Rick Baker, chief revenue officer at OTTO Motors. "Our goal is to provide better technology for our customers so they can better serve theirs."
The OTTO even helps the Sunview impress customers and close deals.
"Our customers see OTTO and recognize that Sunview is a forward-thinking, innovative company," said Oberparleiter. "It makes them want to do business with us."
Learn more about OTTO Motors at MODEX Booth #10019 March 9-12 in Atlanta.
About OTTO Motors
OTTO Motors is the industrial division of Clearpath Robotics. OTTO Motors provides self-driving technology for material handling inside manufacturing facilities and warehouses. OTTO is trusted for mission-critical deliveries spanning the most demanding of industrial environments. Seventy-five percent of robots deployed by OTTO Motors are located within Fortune 500 companies. For more information, visit www.ottomotors.com.
Featured Product
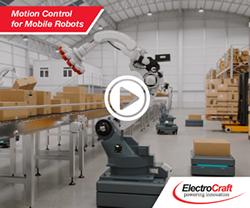
ElectroCraft's Motion Control for Mobile Robots
ElectroCraft is showcasing its award-winning mobile robot technology including their powerful and compact wheel drives, high-torque-density brushless DC motors, precision linear actuators as well as servo motor drive technology at a variety of conferences and tradeshows including the Boston Robotics Summit. Robotics Summit is the premier symposium for the sharing of ideas, technology, and market developments for robotic technologies across industries. Beyond a showcase and pitch of product, ElectroCraft is eager to participate in the collaborative discussion of challenges and opportunities that will shape the near and long-term robotic marketplace.