New Universal Robots Interface Enables Fast Cobot Deployment for Injection Molding Applications
With the Injection Molding Machine Interface (IMMI), the collaborative robots leader has launched a user-friendly and quick solution for plastics manufacturers to integrate Universal Robots with injection molding machines.
Plastics manufacturers are increasingly turning to collaborative robots to tend injection molding machines. With the launch of the new Injection Molding Machine Interface (IMMI), Universal Robots makes the communication between its e-Series cobots and injection molding machines fast and easy. IMMI supports injection molding machines with EUROMAP 67 and SPI AN-146 communication interfaces.
"Injection molding machines have many inputs and outputs to manage the complexities of the molding process"
The global market for collaborative robots in the plastics and polymers industry is expected to grow exponentially over the next five years, from $250M in 2020 to $1.5B in 2025. According to BIS Research, 15 percent of all cobot applications in 2020 will be within injection molding, automating tasks such as placing inserts into molds and moving parts through post-mold processes. These are tasks that require high repeatability, complex motions, and demanding angles, making them perfectly suited for the six-axis cobots from Universal Robots (UR). The cobots can be mounted on top or beside an injection molding machine and they can work alongside human operators without safety cages (subject to risk assessment), saving valuable space on the workshop floor.
"Injection molding machines have many inputs and outputs to manage the complexities of the molding process," says Joe Campbell, senior manager of applications development at Universal Robots. "Standardized interfaces allow for ease of integration and exchangeability. With the IMMI, we give the manufacturer the ability to set up, program and control the entire application cycle through the UR cobot's teach pendant. Combine this with the positioning flexibility and the additional degrees of freedom found in UR cobots compared to traditional cartesian robots, and you have a very powerful solution."
The IMMI is installed in the UR cobots' control box in less than ten minutes, providing deep integration with the robot system, including safety functionality, and leveraging the e-Series cobots' control box expansion port for easy mounting and cable management. An IMMI template for the Universal Robots Polyscope operating system is provided for easy use in the programming tree. IMMI is now available through Universal Robots' rapidly expanding UR+ platform of products certified to work seamlessly with UR cobots.
Download product videos and images here:
urrobots.com/IMMI
About Universal Robots
Universal Robots (UR) was founded in 2005 to make robot technology accessible to all by developing small, user-friendly, reasonably priced, flexible collaborative robots (cobots) that are safe to work with. Since the first cobot was launched in 2008, the company has experienced considerable growth with the user-friendly cobot now sold worldwide. The company, which is a part of Teradyne Inc., is headquartered in Odense, Denmark, and has regional offices in the United States, Germany, France, Spain, Italy, UK, Czech Republic, Poland, Hungary, Romania, Russia, Turkey, China, India, Singapore, Japan, South Korea, Taiwan and Mexico. In 2019, Universal Robots had a revenue of USD 248 million. For more information, please visit www.universal-robots.com.
Featured Product
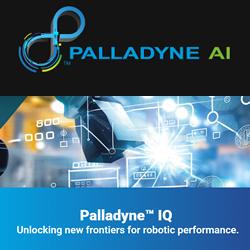