ATI Announces Free Webinar with 3M and Unveils new Material Removal Tools
ATI and 3M co-present “Three Pillars of Successful Material Removal” on Thursday May 14 at 12pm ET
APEX, N.C. April 30, 2020 - ATI Industrial Automation and 3M will co-present a free webinar, "Three Pillars of Successful Material Removal," on Thursday, May 14, 2020 at 12pm ET. The event, hosted by the Robotics Industries Association, will identify key concepts for successful robotic material removal. Presentations by ATI's Material Removal Product Manager, Dan Merritt and 3M Global Applications Engineer, Sarah Mullins, feature real-world examples of the benefits of robotic material removal and illustrate how common challenges are overcome with the right application design. Through the webinar, ATI and 3M will demonstrate how a comprehensive understanding of your process can help you choose the best equipment and abrasives for the job.
<
ATI dives deeper into material removal processes with new solutions for force control and adjustable speed precision deburring. The new PCFC Passive Compliant Force Control Device provides an open platform to incorporate passive compliance into applications that use rigid material removal tools. The pneumatically actuated device mimics the responsiveness of a manual process while eliminating hazards to workers. The RCE-710 Radially Compliant Electric Tool is a complete electric deburring package that also includes an easy-to-use controller and cabling.
ATI Industrial Automation is working alongside industry partners like 3M to make automation more accessible through developing new solutions and exploring new opportunities. Through listening to customers, understanding shared manufacturing challenges, and creating partnership with industry leaders, ATI is determined to support the growth of robotic material removal.
About ATI Industrial Automation
ATI Industrial Automation is the world's leading engineering-based developer of robotic accessories and robot arm tooling including Robotic Tool Changers, Multi-Axis Force/Torque Sensing Systems, Utility Couplers, Manual Tool Changers, Robotic Deburring Tools, Robotic Collision Sensors and Compliance Devices. Their robotic end-effector products are found in thousands of applications around the world. Manufactured entirely in the USA, ATI products enable customers to achieve a high level of flexibility in robotic automation. Their flagship product is the Robotic Tool Changer, a robotic wrist coupling that locks and unlocks automatically, allowing a single robot to perform many different tasks. ATI products can be found at some of the world's most renowned corporations and organizations including NASA, Ford, Honda and Johns Hopkins University. For more information visit ATI at: www.ati-ia.com.
Featured Product
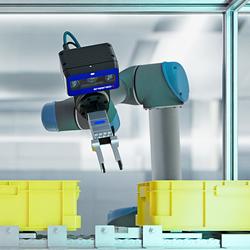