SAFELY SEPARATE STEEL SHEETS WITH FAIL-SAFE MAGNET
The fail safe magnetic separator automatically separates steel sheets of almost any shape, length or width up to a thickness of approximately 4 mm. Also round and asymmetrical shapes. The extremely safe - hence the name ‘fail-safe' - sheet separator automatically switches to the off position even if the compressed air supply is interrupted. Even at full load at maximum stacking height. The separator is equipped with very powerful neodymium magnets and can be switched on and off pneumatically using a new patented system. The permanent magnetic force does not degrade and is guaranteed for decades. See how it works: https://youtu.be/V-dEDZPCXXA
Goudsmit presents a recently developed fail-safe magnetic sheet separator. It provides automatic separation of steel sheets up to a thickness of approximately 4 mm. The separator is equipped with very powerful neodymium magnets and can be switched on and off pneumatically using a new patented system.
This switching is done quickly by rotation of the magnets. The maintenance-free sheet separator is the only one of its kind with a spring-actuated off position. The extremely safe - hence the name ‘fail-safe' - sheet separator automatically switches to the off position even if the compressed air supply is interrupted. Even at full load at maximum stacking height.
The magnet cannot accidentally remain switched on during maintenance either. That's something you ordinarily can't see, and it often leads to industrial accidents. With the red indicator you can see from a distance whether the magnet is switched on.
This provides extra safety, In contrast to fixed sheet separators, switchable sheet separators also allow interim changeover of products during a set process. It is possible to separate steel sheets of almost any shape, length or width. Even round and asymmetrical shapes. The permanent magnetic force does not degrade and is guaranteed for decades.
AUTOMATED PROCESSES
In combination with the swivel arm, this system is also height adjustable. Magnetic sheet separators are used in sheet processing industries and in robotized production cells for the production of welded assemblies. Robots use magnetic grippers to pick up large sheet metal parts and position them on a welding table. Because the steel sheets are oiled, they stick together and the robot occasionally picks up two sheets at the same time.
As a consequence, the second steel sheet may release halfway across the welding table and fall. This causes tremendous damage in high-tech environments, where the welding table is often equipped with sensors, transducers and actuators. Moreover, the double insertion of two steel sheets that are stuck together can cause extensive damage to a die.
Through the use of neodymium sheet separators, the sheets are separated from each other despite the oil film, after which the robot can lift them from the stack, one at a time. The fail-safe sheet separator also has the option of on/off detection by means of a pluggable plug & play system.
PNEUMATIC OPERATION
The compressed air-operated sheet separators increase safety and reduce costs when stacking or changing stacks of steel sheets. The magnets separate oiled sheets and even work well when vacuum is present between the steel sheets. Or when the sheets have been pre-processed or polished. In contrast to fixed sheet separators, switchable sheet separators allow interim changeover of products during a set process.
When the upper sheet is removed from a stack, the lower one immediately takes its place. To replenish the stack of steel sheets, the magnetic sheet separators can easily be switched off with a pneumatic valve. After releasing the swivel arm, the magnets rotate away, at which point the stack of sheets can easily be exchanged or replenished
For more information, send a mail to info@goudsmit.eu or call +31(0)40-2213283
Featured Product
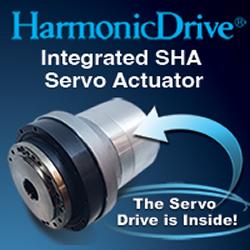