MODULAR MAGNETIC PALLETIZER SAVES EXTRA ROBOT
Goudsmit Magnetics recently redesigned its magnetic palletizer, which now consists of modules that are available in several versions. The maintenance-friendly magnet is suitable for palletizing and depalletizing tins, aerosol cans, canned goods and glass jars with steel lids. The modular construction offers users, such as integrators, packaging companies and producers of food or chemicals, a number of choices that will eliminate the need for an extra robot and save manpower
A lightweight version, for example. Or the choice of a spring suspension unit, which serves as a flexible guideway that prevents product damage and enables correct positioning. The vacuum system and pallet gripper options make it possible for operations such as picking and placing a pallet, separator sheet or layer of cans to be carried out by a single robot. The associated savings result in a quick payback period for this new system. See film here.
DESIGN
The integrated vacuum system is designed for picking up and processing any size and type of separator sheet. The parallel mechanism guarantees a low-maintenance, trouble-free production process, even with non-uniform loads, such as when picking up an uneven layer. The magnet is fitted with several pole systems so that with light tins or aerosol cans the field is stronger at the surface and with heavier loads, like canned goods, the magnetic field is deeper. The palletizer uses pneumatics for easy control and is equipped with sensors for on/off detection. The spring suspension unit makes positioning easy and prevents product damage. It is also equipped with sensors that prevent misalignment (twisting) and jamming, as well as crashing of the robot in unexpected situations. The new design of the palletizer is the result of thorough market research and use of the DFMA methodology (Design for Manufacturing and Assembly).
MAINTENANCE
The magnetic palletizer has a long service life, is very easy to maintain and consumes little air. Any wear parts are easy to replace. The central scissor mechanism consists of two cylinders which ensure that the palletizer is switched on and off evenly and that the plate magnet is activated in one go. This ensures equal application of the magnetic force across the entire surface, which distinguishes Goudsmit palletizers from other types. The company (Goudsmit) supplies the lightweight magnetic palletizer to various customers worldwide. In some locations, the system runs continuously, 24 hours a day. Even then, maintenance is minimal.
See how it works: https://youtu.be/-jmGU5eJqGM
Featured Product
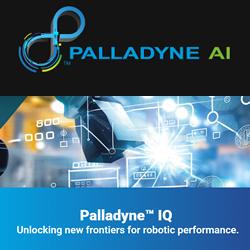