UltraFlex induction heating a steel cylinder prior to epoxy curing
In a recent test application set up for demonstration purposes, UltraFlex proved the energy- and cost- efficiency of induction heating for a steel cylinder, prior to using it for epoxy curing. The demo setup had been done per request of a plastics manufacturer looking to switch from resistance heating to induction heating, to reduce heating cycle times and achieve increased repeatability.
In a recent test application set up for demonstration purposes, UltraFlex proved the energy- and cost- efficiency of induction heating for a steel cylinder, prior to using it for epoxy curing. The demo setup had been done per request of a plastics manufacturer looking to switch from resistance heating to induction heating, to reduce heating cycle times and achieve increased repeatability.
The goal of the test application was to evenly heat a steel cylinder to 250°F (121°C) prior to using it for epoxy curing. Maintaining the temperature below 350°F had been critical for this process, to avoid burning of the epoxy. Hence, using an induction heating solution with a digital temperature control had been a must for this customer scenario and a key reason why the manufacturer turned to UltraFlex.
Considering the size, shape and material of the workpiece, UltraFlex engineers considered the UltraFlex UltraHeat SM induction heater as most appropriate for this application case. UltraHeat SM is a 5 kW induction heating system that operates with either a water-cooled or air-cooled remote heat station. It is easy to tune to a wide range of loads and coils and has multiple user programs and programmable parameters.
Using UltraHeat SM, the induction heating for the sample part had been successfully completed. The target temperature had been successfully reached, in a fraction of the usual heating time needed and a resin compound could then get injected into the part for curing. Energy savings in this process had been considerable, since induction heating can turn up to 90% of the energy into heat into the part. Thanks to the elimination of open flame, this had been a completely green process - eliminating smoke, waste heat, and noxious emissions. Finally, the process had been fully safe for the operator and not dependent on the operator skill. When implemented on the production line, it would ensure repeatability and consistent results every time.
Find out more at:
https://ultraflexpower.com/
Contact us at:
+1.631.467.6814
uptnews@ultraflexpower.com
About UltraFlex Power Technologies:
UltraFlex Power Technologies (ultraflexpower.com) offers the most advanced and innovative digitally controlled induction heating equipment in the industry. Its compact modular and flexible systems are used for a wide variety of induction heating, casting and melting applications.
Featured Product
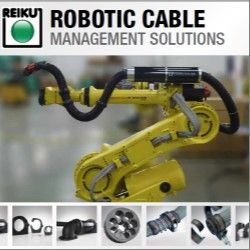