UltraFlex induction brazing copper tube to brass diverter at ~1500 °F (815 °C) within mere 30 sec
This demo scenario proved that induction-based brazing is more time- and cost-efficient compared to torch-based brazing. Thanks to the ability to program UltraFlex induction heating equipment, the customer could achieve perfectly consistent and repeatable results, not dependable on the operator skills.
The time-efficient, cost-efficient and environmentally clean induction brazing for copper and brass parts has recently been demonstrated by UltraFlex Power Technologies. UltraFlex - a major manufacturer of advanced, digitally controlled induction heaters, set up this demonstration per request of a manufacturer from the Appliances industry.
The manufacturer was looking to evaluate the replacement of traditional, torch-based brazing for a copper and brass assembly with induction brazing. Among his main goals were achieving more consistent brazing results, independent from the operator skills, time- and cost-efficiency, along with setting up a cleaner, environmentally safe process.
Due to uniform heating required in difficult to reach areas, UltraFlex engineers recommended the use of mobile brazing equipment like UltraFlex UBraze. UBraze comes with a hand-held brazing gun and allows easy access to any part of the assembly. Thanks to a custom, C-shaped induction coil, the operator could move the heating freely around the joints.
The brazing process had been started by applying brazing flux to the parts to be joined. Induction heating was then applied close to the copper pipe, so no damage would be done to the brass assembly threads. The brazing gun had then been frequently rotated so the heat and alloy flow would distribute evenly. Thanks to Argon blown onto the joint, any residual flux had been removed.
At power of 10.75 kW and target temperature of ~1500 °F (815 °C), it took mere 30 seconds to accomplish this induction brazing process. The result was a precise, reliable and completely clean joint.
This demo scenario proved that induction-based brazing is more time- and cost-efficient compared to torch-based brazing. Thanks to the ability to program UltraFlex induction heating equipment, the customer could achieve perfectly consistent and repeatable results, not dependable on the operator skills. Finally, due to the lack of open flame, the induction-based brazing process would be completely safe - both for the operator and for the environment, with no smoke or noxious emissions.
Find out more at:
https://ultraflexpower.com/
Contact us at:
+1.631.467.6814
uptnews@ultraflexpower.com
About UltraFlex Power Technologies:
UltraFlex Power Technologies (ultraflexpower.com) offers the most advanced and innovative digitally controlled induction heating equipment in the industry. Its compact modular and flexible systems are used for a wide variety of induction heating, casting and melting applications.
Featured Product
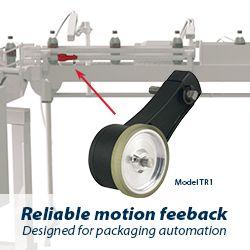