TCL Deploys ForwardX AMRs for World’s First 5G-Enabled AMR Project
The 5G+ Initiative deployed Max 300 Lift AMRs for autonomous material handling
BEIJING, CHINA - Mar. 23, 2021 - The Huizhou factory of Chinese multinational electronics company TCL, specializing in surface-mount technology processes, has installed dozens of ForwardX Max 300 Lift Autonomous Mobile Robots to automate the movement of materials across the production facility. So far, the project has resulted in improved productivity across the production process, less labor dependency for material handling, and a quicker inventory turnover. The AMRs connect and communicate through a 5G network which was set up as part of TCL's 5G+ Smart Factory Initiative.
Located in the Huizhou Zhongkai High-tech Development Zone, TCL's Operation Center serves as the central point of TCL's global supply chain and manufacturing. Boasting the second largest production capacity in the world, the facility looked towards 5G and intelligent robotics to elevate its performance to a new level.
"We believe in and promote the use of intelligent automation, such as AMRs, to support our factories globally by empowering their operations and automating unfulfilling work," said Caijun Zhao, Head of the President's Office for TCL Industries Holdings. "The project (with ForwardX) has been successful so far with seamless collaboration between the AMRs, workers, machines, and loading carts."
Before beginning the project, TCL's management identified 4 main pain points to tackle in the supply chain management of the TCL Operation Center:
- Lack of flexibility: The storage of vital materials was scattered across the facility and, with the seasonal and fluctuating nature of demand, this made changing production processes slow and more complex.
- Network issues: Using Wi-Fi networks across the facility caused a number of blind spots which made operational visibility. The factory wanted a real-time view into and control of their intralogistics processes.
- Dependency on manual processes: A low level of automation meant that most material handling tasks were carried out by factory operators. This resulted in high labor costs and left TCL vulnerable to shifting trends in wages and labor availability.
- Facility complexity: Full of people, moving equipment, production machinery, and material carts, the SMT workshop was a complex environment that made errors commonplace. Furthermore, due to its complexity, the facility was unable to improve efficiency.
TCL completed the project rollout in March 2020 with China Mobile acting as the network service provider and ForwardX Robotics as the intelligent automation provider. As the world's first 5G-enabled AMR project, TCL's collaboration with ForwardX has been recognized across China as the first of its kind with it winning MIIT's Bloom Cup, an accolade given to projects promoting the commercial 5G applications.
In order to achieve unmanned movement, material flow through the facility consists of the following steps:
- Using 5G, TCL's Manufacturing Execution System (MES) pushes production plans out across the facility;
- The lineside warehouse picks, prepares, and organizes materials according to the production plan;
- The lead time and safety stock levels are set according to production capabilities and AMRs are triggered to deliver material to machinery;
- AMRs automatically navigate to the designated pick-up point where they autonomously dock to and lift material carts, before traveling across the facility;
- At specific drop-off points, the AMRs stop and await a corresponding factory operator who removes the required materials and confirms receipt through the onboard GUI;
- Once a batch is complete, the MES triggers the AMRs to travel to machines to pick up finished goods.
- The AMRs travel to the pick-up location and picks up the finished goods before traveling to the warehouse.
When considering the solution, the facility's management made safety a top priority for evaluating solutions. With a large workforce operating across a busy environment, TCL needed a solution that could offer comprehensive safety features to avoid accidents and keep their staff protected. Offering 360-degree obstacle detection and avoidance through laser- and vision-based sensing, ForwardX's Max 300 Lift robots offered the kind of safety guarantees that the global electronics manufacturer was looking for.
"When considering solutions, safety is an important factor for us, because our production lines consist of a lot of machines and our environment is highly dynamic with a lot of moving pieces, such as material carts," said Zhengwei Cai, Project Manager and Senior Engineer in the facility. "Therefore, obstacle avoidance and safety functions are very important to us. With ForwardX, the AMRs calculate optimal routes and automatically detect, identify, and avoid collisions with any kind of obstacle."
After such positive results for the 5G Smart Factory initiative, TCL is evaluating the use of more ForwardX mobile robots for intralogistics workflows, such as raw material delivery, work-in-process transfer, and finished goods storage, in their other production locations. The goal to achieve unmanned material flow through their manufacturing facilities remains strong and TCL will continue to work closely with ForwardX to reach industry 4.0.
About ForwardX Robotics
ForwardX Robotics is a leading innovator in the fields of Artificial Intelligence and Robotics that develops an intelligent mobile robotics platform designed to automate material handling in logistics, manufacturing, and retail environments. With a team of over 200, 10 international patents, and more than 170 patents pending, ForwardX continues to innovate with the mission of empowering supply chains to deliver the next generation of industry. For more information, visit forwardx.com.
About TCL
TCL empowers customers to enjoy more. With a lineup of award-winning televisions, audio products, mobile devices, and appliances, TCL takes pride in delivering meaningful experiences by combining thoughtful design and the latest technology. As one of the world's largest consumer electronics brands, its extensive manufacturing expertise, vertically integrated supply chain, and state-of-the-art panel factory, helps TCL deliver innovation for all. For additional product information, please visit www.tcl.com for the full portfolio.
TCL is a registered trademark of TCL Corporation.
Featured Product
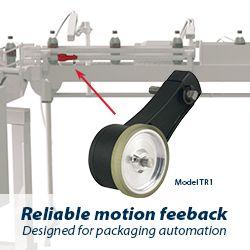