UltraFlex performing 25-second induction debrazing of a carbide tooth from steel body
When used on the line, this induction de-brazing process would ensure time- and cost-efficient tip removal, resulting in higher productivity and lower costs compared to torch-debrazing.
The time- and cost-efficient removal of a carbide tooth from the steel body of a pavement cutting tool has recently been demonstrated by UltraFlex Power Technologies. UltraFlex - a leading manufacturer of digitally advanced induction heaters - performed the demo per request of a customer from the Automotive & Transportation industry, aiming to showcase the efficiency and safety of induction debrazing compared to torch-based debrazing.
Carbide-tipped tools are frequently used when hardness and durability of the tool is a must. The carbide used for tipping in this case is tungsten carbide, renown for being able to withstand wear and high-impact forces.
Tungsten carbide had also been used for tipping the customer's pavement cutting tool but the customer was in need of a much faster, efficient and repeatable tip-removal process. The tip size was 1.27 cm (0.5 inches) and the tool body was made of steel.
An induction heater from the UltraFlex UltraHeat W series had been considered most appropriate for this induction de-brazing scenario. UltraHeat W are advanced, cost-effective 5-15 kW Induction heaters utilizing the latest switching power supply technology. They are configured to operate with external Heat Stations allowing output connections to be available from all sides.
At 5 KW of power used, it took mere 25 seconds to heat the carbide tip and the joint that connected it to the steel body. The tip and joint could then be easily removed from the body using pliers.
When used on the line, this induction de-brazing process would ensure time- and cost-efficient tip removal, resulting in higher productivity and lower costs compared to torch-debrazing. In addition, the customer would achieve a high-quality and high-repeatability removal process, with no dependency on the operator skills. Last but not least, the customer would benefit from an operator-safe and environment-safe process, with no noxious emissions.
Find out more at:
https://ultraflexpower.com/
Contact us at:
+1.631.467.6814
uptnews@ultraflexpower.com
About UltraFlex Power Technologies:
UltraFlex Power Technologies (ultraflexpower.com) offers the most advanced and innovative digitally controlled induction heating equipment in the industry. Its compact modular and flexible systems are used for a wide variety of induction heating, casting and melting applications.
Featured Product
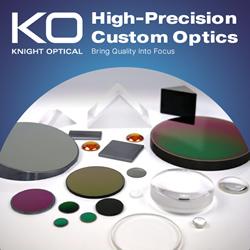