UltraFlex using induction to preheat steel shovel forms to 1742°F/950°C within less than 5 seconds
The efficient usage of induction heaters for preheating steel shovel molds has recently been demonstrated by UltraFlex Power Technologies. Being a leading manufacturer of advanced induction heater solutions, the company is frequently showcasing the high efficiency of induction heating compared to traditional heating methods, for a rich variety of industrial applications.
The efficient usage of induction heaters for preheating steel shovel molds has recently been demonstrated by UltraFlex Power Technologies. Being a leading manufacturer of advanced induction heater solutions, the company is frequently showcasing the high efficiency of induction heating compared to traditional heating methods, for a rich variety of industrial applications.
In this demo case, a potential customer from the Dies and Molds industry was looking to replace their current gas furnace-based preheating method with induction heating, to achieve faster heat cycles, repeatability and a uniform heating temperature. The customer was manufacturing steel shovels and the process required to preheat metal billets to a target temperature of 1742°F/950°C, before they were further processed for bending and shaping. The target temperature had to be reached within less than 5 seconds.
For this heating process UltraFlex engineers recommended the use of an Ultraflex SmartPower™ system. UltraFlex SmartPower™ Compac are a breakthrough innovation in induction heating. The latest SiC transistor technology and proprietary digital control algorithms they use ensure optimal performance and maximum efficiency in a wide frequency range.
UltraFlex designed a custom induction coil for this heating process, so multiple shovel molds could be preheated at the same time and the productivity largely increased. With SmartPower™ turned on, it took less than 5 seconds for all steel molds to reach the target temperature of 1742°F/950°C! The customer had all target parameters met, but also achieved great thermal efficiency, thus substantially cutting down the energy consumed for the heating process. The heating times were decreased, and all heated items achieved uniform temperature.
If used on the production line, this induction heating process would ensure increased productivity and high-quality, repeatable results, independent of the operator's skills. This would also be a safe process - both for the operator and the environment - with no smoke, waste heat, and noxious emissions.
Find out more at:
https://ultraflexpower.com/
Contact us at:
+1.631.467.6814
uptnews@ultraflexpower.com
About UltraFlex Power Technologies:
UltraFlex Power Technologies (ultraflexpower.com) offers the most advanced and innovative digitally controlled induction heating equipment in the industry. Its compact modular and flexible systems are used for a wide variety of induction heating, casting and melting applications.
Featured Product
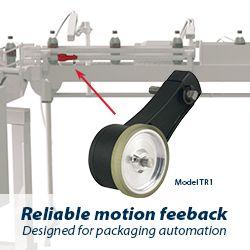