DC Motor and DC Gear Motor Selection Tips
4 Tips For Selecting a DC Motor or Gear Motor For Any Application
As world-leading DC Motor and Gear Motor design experts, we are here to get your next project "moving". Our team of dedicated application engineers can assist and answer any questions you may have, just get in touch or give us a call.
Tip # 1: Determine Your Speed, Torque and Voltage First
The three main specifications you will need to know for any DC motor application are voltage, speed and torque. Once these aspects are determined, you are now ready to get started on your journey to select the ideal motor solution. The key is to use a motor that is operating at or near its maximum efficiency.
Motor voltage should also be defined at the start of the motor selection process. Motor voltage will be determined by your electrical power source, for example a 12-Volt battery or power supply.The nominal voltage for DC motors is typically either 12 or 24VDC.
Rotational speed is important for any motion control application. The rated or on-load motor speed is how fast a DC motor will operate once a load is applied. The constant speed and maximum speed that the motor needs to operate at are important to know.
Motor torque is the amount of load the motor's output shaft can overcome at a given point. The torque and speed of a motor are directly related to one another, as one increases the other decreases. The rated torque, or on-load torque, needs to be defined just like the speed. Another important aspect of torque is the motor's stall torque or peak torque.
The relationship between torque and speed can be best understood by evaluating a motor's performance curve, commonly found with the motor specification.
Choosing a motor or gear motor that meets both your speed and torque requirements is crucial in selecting an efficient motor for your application.
Tip # 2: Balance Size vs. Performance
Proper motor size is important for every application but it can become an issue if a certain performance is required. Typically, larger motors are more powerful than their smaller counterparts. Depending on your application requirements, you may have to sacrifice certain performance characteristics to help accommodate the size constraints.
By utilizing different types of motors and motor technologies, like brushless motors or motors with permanent magnets, there are endless possibilities to help meet the size constraints for the majority of applications.
Tip # 3: Gear Motors Offer More Torque
Sometimes you need more torque than is physically possible to get out of a standard DC motor. Utilizing a DC gear motor will result in increased torque and reduced speed, which is all dependent on the gear ratio that is used. There are 3 basic types of gear motors: spur gear motors, planetary gear motors, and worm gear motors. Each gearhead type has its own distinct advantages. You can add a gearhead to stepper motors, brushless DC motors, as well as brushed DC motors.
Tip # 4: Define your Duty Cycle
Your duty cycle will dictate which motor type is best for your application or device. Operating times and dwell times, as well as directional rotation, are key aspects of your duty cycle. The duty cycle should be defined at the beginning of the motor selection process.
Intermittent duty cycles are encouraged for most industrial applications to help extend the useful life of a motor or gear motor. Continuous use is still acceptable but you need to make sure the motor is operating at its peak efficiency.
Discuss your requirements with our engineers today! Our team of dedicated application engineers are here to assist at any stage throughout your design cycle. Feel free to utilize our Industrial Motor Selection Tool to get started! ISL Products offers a wide range of value added component solutions, so contact us today!
Featured Product
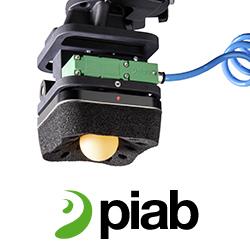
Piab's Kenos KCS Gripper
Piab's Kenos KCS gripper enables a collaborative robot to handle just about anything at any time. Combining Piab's proprietary air-driven COAX vacuum technology with an easily replaceable technical foam that molds itself around any surface or shape, the gripper can be used to safely grip, lift and handle any object. Standard interface (ISO) adapters enable the whole unit to be attached to any cobot type on the market with a body made in a lightweight 3D printed material. Approved by Universal Robots as a UR+ end effector.