UltraFlex demonstrates induction annealing of stainless steel cylinder for the automotive industry
This application test proved that by using induction, the customer's annealing process could be fully automated, achieving a short heat cycle and consistent, repeatable results, independent of the operator skills.
UltraFlex - a leading manufacturer of digitally controlled induction heaters - has recently demonstrated the efficiency of using induction heating in yet another customer application.
The customer - a manufacturer of automotive parts - was looking to evaluate the usage of induction heating to anneal and thread-roll stainless steel tubes. He was aiming at increasing the productivity of this process, with target productivity rates of 10-20 seconds per heat cycle.
For the test application set up by UltraFlex engineers, the customer provided a cut sample with dimensions 1'' OD x 1.50" long x 0.11" wall (2.54 cm x 3.81 cm x 0.28 cm). He was looking to evaluate the results achieved at different heating temperatures close to the target temperature of 1900°F (~1038°C), so he could identify the best temperature enabling further, easier forming of the heated part.
For this customer application UltraFlex engineers recommended the use of a 5 KW induction heater from the UltraFlex UltraHeat SM series, along with a 6-turn helical induction coil. UltraHeat SM 5 are compact and easy-to-use 5kW induction heaters. They are reliable, modular systems, easy to tune to a wide range of loads and coils.
By using UltraHeat SM 5, UltraFlex applied temperatures of 1500, 1600, 1700, 1800, and 1900°F (~815, ~871, ~927, ~982, ~1038°C) to the heated parts, so the customer would be able to evaluate the best temperature for his heating application. Thanks to using a pyrometer, the engineers guaranteed that the maximum annealing temperature of 1900°F would not be exceeded.
It took less than 30 seconds to apply each of the tested heating temperatures, at the maximum power output of 5 kW.
The test setup concluded that a custom-designed heating coil was critical for this test scenario. It would ensure even heat distribution along the whole length of the heated part, as well as optimal heating settings. Thus the annealing process could be fully automated, achieving a short heat cycle and consistent, repeatable results, independent of the operator skills.
Thanks to the fast, time- and energy-efficient test setup, the customer was able to easily evaluate the induction heating parameters required as well as the productivity increase he could expect.
Find out more at:
https://ultraflexpower.com/
Contact us at:
+1.631.467.6814
uptnews@ultraflexpower.com
About UltraFlex Power Technologies:
UltraFlex Power Technologies (ultraflexpower.com) offers the most advanced and innovative digitally controlled induction heating equipment in the industry. Its compact modular and flexible systems are used for a wide variety of induction heating, casting and melting applications.
Featured Product
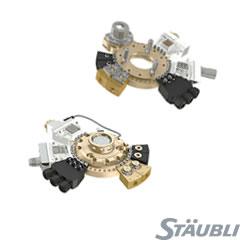
Stäubli robotic tool changer solutions
Stäubli is a pioneer in the construction and development of robotic tool changing systems. Our customers benefit from our many years of expertise in all industry sectors, as well as our modular product concept, which offers three efficient solution paths: MPS COMPLETE offers preconfigured robotic tool changers for immediate use. MPS MODULAR allows the user to determine the configuration, while MPS CUSTOMIZED allows the construction of special, application-specific systems.