UltraFlex demonstrates 5-second induction brazing for steel tube to gold wire
An UltraFlex demo application recently set up per request of a potential customer from the Oil & Gas industry helped evaluate the best induction heating equipment and heating parameters for the brazing of a stainless steel and gold wire assembly.
An UltraFlex demo application recently set up per request of a potential customer from the Oil & Gas industry helped evaluate the best induction heating equipment and heating parameters for the brazing of a stainless steel and gold wire assembly. UltraFlex Power Technologies is a leading provider of advanced, digitally controlled induction heaters and as such is frequently setting up test applications for the purpose of showcasing the efficiency of induction heating for a host of manufacturing applications.
In this test scenario, the customer was looking to replace their current resistance brazing process with an induction-based one, to achieve higher productivity, better control on the process and high-quality, reliable brazing results with far less losses of expensive parts. The parts to be brazed were a special wire assembly, including a stainless steel outer jacket, an inner gold wire and a glass center conductor. The stainless steel tube had a 0.0625" (0.159 cm) OD and the gold wire had a 0.011" (0.028 cm) OD. The goal was to braze a very tiny area of the tube - 0.50-1″ (1.27-2.54 cm) in length, using a braze alloy.
The customer-required maximum brazing temperature was 1250°F (~677°C), with a targeted heat cycle of maximum 5 seconds.
For this heating scenario UltraFlex engineers used a 5 kW induction heater from the UltraFlex UltraHeat SM series. UltraHeat SM are compact and easy to use 5 kW induction heaters that operate with either a water-cooled or air-cooled remote heat station. They are reliable, modular systems, easy to maintain and service.
At 600 W of power applied, the brazing was fully complete at 1112°F (600°C), with a heat cycle as short as 5 seconds. The result was a high-quality, reliable brazing joint, achieved within the target temperature and heating time.
After reviewing the output parameters of the test application, UltraFlex engineers concluded that a 2 KW induction heater would efficiently work for this heating scenario, while being more affordable for the customer. In addition, further fine-tuning of the heating parameters would allow to shorten the heat cycle even more, while providing the same high quality of the joint. Finally, by using induction heating the customer could ensure consistent, repeatable results every time and achieve full automation for the process.
Last but not least, induction heating would ensure a clean and safe process - safe for the operator and the environment - due to the lack of open flame and noxious emissions.
Find out more at:
https://ultraflexpower.com/
Contact us at:
+1.631.467.6814
uptnews@ultraflexpower.com
About UltraFlex Power Technologies:
UltraFlex Power Technologies (ultraflexpower.com) offers the most advanced and innovative digitally controlled induction heating equipment in the industry. Its compact modular and flexible systems are used for a wide variety of induction heating, casting and melting applications.
Featured Product
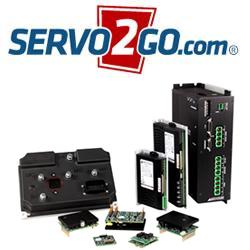