KNEO Automation’s Remote Machine Monitoring Software Utilizes IoT to reduce Machine Downtime
Downtime is a major threat to any manufacturing business. Traditional data collection of downtime events was completely manual. Paper forms on clipboards, spreadsheet-based analysis, and formulas were utilized to gather downtime data.
Warje, Pune, Maharashtra, November 14, 2022: Downtime is a major threat to any manufacturing business. Traditional data collection of downtime events was completely manual. Paper forms on clipboards, spreadsheet-based analysis, and formulas were utilized to gather downtime data. Once this data was gathered, it needed to be accumulated, entered into a spreadsheet, and presented in a consumable report to managers and others who could make decisions. Manual, as well as the partially automated recording of downtime events, lacked the advantage of real-time analysis. This takes us to a truly paperless approach to reduce machine downtime.
Unexpected equipment failures can lead to expensive interruptions in your process flow, damage to equipment and product losses. The risk and cost of unplanned downtime are also high, as there is no other way to forecast the necessity for maintenance or repairs, other than the utilization of historical patterns.
Hence manufacturers need to know the current status of all machines on a line and some additional data about each machine to harness the data effectively. And this is where KNEO Automation's IoT remote monitoring solution helps to monitor all of the machine's real-time data remotely.
Poor processes and insufficient maintenance are also some causes of unplanned downtime. On the other hand, planned machine downtime is usually assigned to maintenance, cleaning, and upgrading equipment. Due to this manufacturer needs to deal with high maintenance costs and should take an advantage of a new strategy.
The bigger the plant, the more essential tracking production efficiency and downtime become. The method of manual tracking is generally used, but it is rapidly decreasing with the adoption of predictive maintenance technology. It provides a simple way to analyze machine performance, thus fine-tuning OEE and reducing downtime. Predictive maintenance is a dynamic strategy that estimates equipment's condition with the help of constant monitoring. The major goal is to utilize real-time data to identify component failures early, reduce unplanned downtimes and stay away from expensive repairs.
Not only does its quick visibility help operators and managers to rectify and prevent machine downtimes, but they can also get several production reports and trends likewise downtime reasons, OEE of machines with availability, duration of downtime, shift-wise downtime, performance as well as quality.
With KNEO Automation, downtime can be utilized in easy-to-read, relevant reports and Pareto charts. The dashboard drives prompt actionability and visibility on the shop floor. Real-time machine health monitoring assists managers and operators to keep machines running without failure or downtime.
Links
To know more about how to prevent machine downtime with KNEO Automation's machine monitoring solution, please visit us at: http://bit.ly/3O84vX8
About Kneo:
Kneo has been engaged in the field of industrial automation in various sectors of the economy like Automotive, Food and beverages, Textile, Process, etc. Along with Automation operations, they are also providing solutions in the IT- OT domain. Kneo helps in automating processes with various Industrial automation services. Their Industry 4.0 solution includes a Performance monitoring system, an advanced scheduling module, a track and trace module, maintenance management, etc.
Featured Product
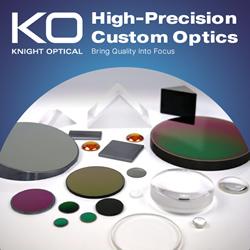