STILRIDE introduces 3D printing to “industrial origami” manufacturing arsenal
STILRIDE - the Swedish startup known for its origami-inspired approach to electromobility design and manufacturing - is joining forces with French-Swedish robotics company ADAXIS to introduce 3D printing capabilities to its suite of sustainable manufacturing tech.
Until now, STILRIDE has had to source a number of component parts for the SUS1's early prototypes - such as hinges, fenders and side covers - from external suppliers. These are small and complicated parts that STILRIDE's engineers cannot create using STILFOLD.
But the new partnership with ADAXIS means STILRIDE will be able to produce a number of these complex components out of steel using additive manufacturing. ADAXIS's software enables engineers to programme a robotic arm to 3D print large and complex steel, plastic, composite and concrete parts quickly, whilst significantly reducing costs and material waste. Damaged parts can also be repaired efficiently using the same technology.
The technology will simplify the production process for STILRIDE's first e-motorbike substantially, bringing additional robot-powered manufacturing capabilities in-house and further improving the material efficiency of each bike.
The partnership also brings powerful new additive manufacturing capabilities to STILRIDE's existing suite of manufacturing technology, called STILFOLD, which will eventually be made available to designers and manufacturers who wish to licence it to build their own work.
Already, the STILFOLD technology is being used by Polestar to develop the world's first climate neutral car; and by Swedish space innovation agency I.S.A.A.C to explore how curve folding could be used for construction in outer space.
Jonas Nvyang, CEO and co-founder at STILRIDE, comments -
"We're excited to be working with fellow Swedish tech innovators ADAXIS to enhance our sustainable manufacturing technology offering. The team at ADAXIS has a huge amount of knowledge and experience in robotics and optimising robotic construction, so it's great to have them on board to strengthen the capabilities of our tech. Not only will their technology improve the sustainability, speed and cost-efficiency of producing the SUS1, but it will also help us reach our ultimate goal of rolling out a fully distributed production model where the construction of our products can be fully automated, powered by robotics technology."
Emil Johansson, co-founder at ADAXIS, comments -
"Using robotization we can push the limits of what can be manufactured using 3D technology, both in terms of size and shape. The challenge is that programming robots for 3D is significantly more advanced and complex than for normal welding jobs. Our goal is to speed up the manufacturing process and make it more intuitive, even when it comes to really complex projects, so that everyone can benefit from this technology.
"We're excited to partner with STILRIDE to supercharge their origami-inspired manufacturing technology with 3D printing capabilities, and enable them to maximise the potential for robotic automation to speed up and simplify the way they manufacture."
Featured Product
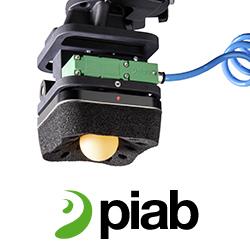
Piab's Kenos KCS Gripper
Piab's Kenos KCS gripper enables a collaborative robot to handle just about anything at any time. Combining Piab's proprietary air-driven COAX vacuum technology with an easily replaceable technical foam that molds itself around any surface or shape, the gripper can be used to safely grip, lift and handle any object. Standard interface (ISO) adapters enable the whole unit to be attached to any cobot type on the market with a body made in a lightweight 3D printed material. Approved by Universal Robots as a UR+ end effector.