BitFlow Publishes CoaXPress Whitepaper
BitFlow has published a new whitepaper Controlling CoaXPress Cameras from The BitFlow SDK Tools, Configuration File, and APIs to help integrators new to the CoaXPress (CXP) standard integrate CXP cameras into their system infrastructure to shape positive outcomes.
The challenges facing today's machine vision integrators are more complicated and critical than ever before, as they strive to build faster, more accurate, and cost-efficient systems in the wake of changing technology. To that end, BitFlow has published a new whitepaper Controlling CoaXPress Cameras from The BitFlow SDK Tools, Configuration File, and APIs to help integrators new to the CoaXPress (CXP) standard integrate CXP cameras into their system infrastructure to shape positive outcomes.
CoaXPress is the world's fastest standard for professional and industrial imaging applications such as machine vision, medical imaging, life sciences, broadcast, and defense. It is an asymmetric point-to-point serial communication standard that transmits video and still images, scalable over single or multiple coaxial cables. It has a high-speed downlink of up to 12.5 Gbps per cable for video, images, and data, plus a lower-speed uplink of up to 42 Mbps for communications and control.
An invaluable learning tool, the 10-page whitepaper details the flexible CXP tools available in the BitFlow SDK (Software Development Kit), and how they work in concert to meet different application needs. It also provides examples showing the optimization of a CXP machine vision system, accelerated and simplified by the BitFlow SDK.
The publication of the new whitepaper is part of the rollout of the BitFlow Claxon CXP-12 PCIe Gen 3 frame grabber. Download the whitepaper here. chrome-extension://efaidnbmnnnibpcajpcglclefindmkaj/http://www.bitflow.com/PDFs/BitFlowCXPCameraControlWorkflow.pdf
Featured Product
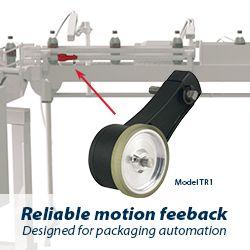