Cutting edge motor and drive technologies from ElectroCraft Inc.
Founded in 1960, ElectroCraft has been providing reliable and efficient FHP motor and motion solutions for over 60 years.
ElectroCraft is a market leading manufacturer specializing in fractional horsepower (FHP) motors and drives. With engineering, manufacturing and value-add operations throughout the U.S., Europe and Asia, ElectroCraft has a large global footprint and serves a diverse range of markets and applications.
Founded in 1960, ElectroCraft has been providing reliable and efficient FHP motor and motion solutions for over 60 years.
FHP motors are typically used in applications where a small amount of power is required, such as in medical and laboratory equipment, robotics and industrial automation. ElectroCraft's range of FHP motors includes AC and DC motors, gearmotors, servo motors, stepper motors, linear actuators and more. ElectroCraft motors are known for their efficiency, durability and precision, making them a popular choice for customers in different industries.
In addition to motors, ElectroCraft also offers a range of servo motor drives and controllers to complement the motor products. These include stepper motor drives, brushless DC (BLDC) motor drives and servo drives, among others. ElectroCraft motor drive platforms are designed to work seamlessly with ElectroCraft motors, providing precise and reliable control for various applications.
ElectroCraft also offers custom design and engineering services, allowing customers to get tailor-made solutions to fit their specific needs.
With a commitment to quality, innovation and customer satisfaction, ElectroCraft has become a trusted name in the FHP motor and motion control industry. Their solutions are known for their durability, reliability and high performance, making them a top choice for customers in various industries.
To better acquaint the reader with the ElectroCraft motor and servo drive product offer, this article will review:
BLDC motor proliferation
The need for more sophisticated (but easy to use) servo motor drives
Servo drive and motor control systems, the decision to buy versus make
The proliferation of BLDC motor technology in an ever-increasing low-voltage and battery-powered world
Of all the FHP motor architectures that ElectroCraft produces, BLDC motor technology continues to increase in demand across most industry segments. BLDC motors provide several benefits in low-voltage DC and battery-powered applications, including:
Increased efficiency
BLDC motors are more efficient than other motor architectures as they are smaller in size, lighter in weight, generate less heat and less friction, which all lead to reduced power consumption, improved battery life and longer run times.
Improved reliability and lower maintenance
BLDC motors have fewer moving parts, and the absence of brushes eliminates the need for frequent maintenance, making them more reliable over time.
Greater power density
Brushless motors can achieve a higher power-to-weight ratio compared to other motor architectures, making them suitable for applications where weight is a concern, such as mobile robotics.
Quieter operation
Brushless motors operate quietly, making them ideal for applications where noise is a concern, such as in medical and laboratory equipment and other sound-sensitive environments.
Increased control
Brushless motors can be precisely controlled by electronic devices, providing greater control over speed, torque and position compared to other motor architectures.
Torque density in BLDC motors
Torque density is another important factor in the design of BLDC motors, as it affects the motor's performance and efficiency. Simply put, torque density refers to the amount of torque that a motor can produce per unit of volume, and ElectroCraft's engineering expertise and decades of design experience produces some of the highest torque-density motors available on the market today.
In the design of BLDC motors, high torque density is desirable because it means that the motor can produce more torque while occupying less space. This is important in embedded applications where space is limited, such as mobile robots, medical devices and laboratory equipment.
Higher torque density also enables the use of smaller, lighter motors without sacrificing performance. This can improve the overall efficiency and performance of the system, as well as reduce its weight and cost.
Moreover, high torque density helps in applications that require fast and responsive motion control, such as in robotics and high-speed machinery. This is because high torque density allows the motor to generate more force in a short amount of time, providing faster and more precise control.
In summary, torque density is a crucial factor in BLDC motor design as it directly impacts the motor's performance, efficiency and versatility. High torque density enables the use of smaller, lighter and more efficient motors, making it an important consideration in the development of advanced applications.
The need for more sophisticated servo drive and motor control technology
To realize the full potential of BLDC motors, more sophisticated servo drive technology is required.
One of the main reasons for this is that BLDC motors require precise control of their phase currents and position feedback to operate efficiently and accurately. This is because BLDC motors operate based on the interaction between the rotor's magnetic field and the stator's magnetic field, and any deviation from the intended current or position can result in reduced performance and efficiency.
Sophisticated servo drive technology can help overcome these challenges by providing advanced control algorithms and feedback mechanisms to ensure that the motor operates at the desired speed, torque and position. This can include features such as field-oriented control (FOC) algorithms, which allow for precise control of the motor's magnetic field, as well as advanced position sensing technologies like encoder feedback and Hall-effect sensors.
Furthermore, sophisticated servo drive technology can also offer other benefits such as improved energy efficiency, reduced noise and vibration, and increased reliability and durability of the motor and drive system.
ElectroCraft servo drives incorporate the above technologies by implementing state of the art hardware designs with advanced software control algorithms that work in concert with a wide range of motor architectures, including ElectroCraft's high-performance BLDC motors.
Regarding motor drive hardware designs, ElectroCraft servo drives are available in a variety of form factors, from stand-alone chassis mount drives to ultra-compact PCB assemblies, to integrated motor drives. If needed, ElectroCraft can provide customized designs based on any of these form factors, and even provide a drive on a chip that can be incorporated into a customer's control platform, if desired.
In addition, a key differentiator of ElectroCraft servo drives is ease of use. The goal is to provide a highly configurable product that is easy to learn, easy to configure, and easy to support, without sacrificing the advanced features and functionality that customers require.
In summary, the need for more sophisticated servo drive technology for BLDC motors arises from the need to achieve precise control over the motor's phase currents and position feedback to realize the full potential of these motors in various industrial and consumer applications.
Servo drive and motor control systems: The decision to make versus buy
Designing and manufacturing your own servo drive or motor control platform can be an attractive option for some companies, but it also comes with several pros and cons that should be carefully considered.
The pros of designing and manufacturing your own servo drive include:
Customization
One of the biggest advantages of designing your own servo drive is that it can be tailored to your specific needs. This can include everything from the motor size and control algorithms to the input/output options and communication protocols.
Control
When you design your own servo drive, you have complete control over the hardware and software that make up the system. This can allow for greater precision and flexibility in controlling the servo motor.
Cost
Depending on the volume of servo drives needed, designing and manufacturing your own may be more cost-effective than purchasing from a supplier. This is especially true if you can use off-the-shelf components and have access to skilled engineers who can design and test the system in-house.
As a customized solution provider, ElectroCraft can offer the same levels of customization and control as mentioned above, while delivering a solution that is also cost-effective.
More importantly, consider the cons of designing and manufacturing your own servo drive, including:
Expertise
Designing and manufacturing a servo drive requires a high level of expertise in electrical engineering, software development and control theory. If your company doesn't have this expertise in-house, you may need to invest in hiring and training new staff or outsourcing the design and manufacturing process to a contractor.
Time
Developing a custom servo drive can be a time-consuming process, especially if you're starting from scratch. This can delay your project timeline and potentially impact your business goals.
Risk
Designing and manufacturing your own servo drive comes with a certain level of risk. There is always a chance that the system won't work as intended, which can result in costly delays, recalls or damage to your brand reputation.
Quality
A reputable custom servo drive supplier will have already invested significant time and resources in ensuring their products meet high-quality standards. If you're designing and manufacturing your own servo drive, you will need to put in the same level of effort to ensure the product is reliable and performs as expected.
In summary, designing and manufacturing your own servo drive can be an attractive option if you have the expertise and resources to do so. However, it also comes with certain risks and challenges that may make purchasing from a reputable servo drive supplier a more practical choice for some companies.
ElectroCraft can eliminate the risks without sacrificing the benefits of having a configured or fully customized drive solution for your motion control application.
Advantages of partnering with ElectroCraft, a single-source solution provider
There are several benefits of using a servo motor and drive from the same manufacturer:
Compatibility
When the servo motor and drive are made by the same manufacturer, they are typically designed to work together seamlessly and are often tested and validated as a complete system. This ensures compatibility and reduces the risk of technical issues arising from compatibility problems.
Ease of integration
Integrating a servo motor and drive from the same manufacturer can simplify the process, as the components are designed to work together and the manufacturer can provide technical support for the entire system.
Technical support
When using components from the same manufacturer, it is easier to receive technical support, as the manufacturer will have a complete understanding of the system and can provide prompt assistance.
Consistent performance
Using components from the same manufacturer can ensure consistent performance, as the servo motor and drive are designed to work together optimally and meet the manufacturer's specifications.
Cost savings
In some cases, purchasing a servo motor and drive from the same manufacturer can lead to cost savings, as the manufacturer may offer discounts for complete systems or bundle pricing.
In summary, using a servo motor and drive from the same manufacturer can result in improved compatibility, ease of integration, technical support, consistent performance and potential cost savings.
Conclusion
ElectroCraft's commitment to quality, innovation and customer satisfaction has helped them establish a strong market position in FHP motors and drives. Specifically, based on market and application demand, ElectroCraft has substantially grown their BLDC motor product offering, and greatly expanded their servo motor drive product to support their wide range of electric motors. ElectroCraft products are trusted by customers in various industries, and they continue to innovate and expand their product offerings to meet evolving customer needs.
About ElectroCraft
ElectroCraft, Inc. is a global provider of dependable, application-engineered fractional-horsepower motor and motion products. Over 1 million ElectroCraft gearmotors are in service worldwide delivering the smooth, controlled power with the high starting torque that mobile platforms require.
OEM customers who are unsatisfied with the limitations of inflexible off-the-shelf products can benefit from ElectroCraft's technical knowledge and customizable product families for a motor and motion system that provides superior reliability and performance at the lowest possible cost. For more information and help finding the right motion products for custom applications, contact ElectroCraft.
Featured Product
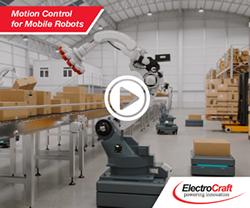
ElectroCraft's Motion Control for Mobile Robots
ElectroCraft is showcasing its award-winning mobile robot technology including their powerful and compact wheel drives, high-torque-density brushless DC motors, precision linear actuators as well as servo motor drive technology at a variety of conferences and tradeshows including the Boston Robotics Summit. Robotics Summit is the premier symposium for the sharing of ideas, technology, and market developments for robotic technologies across industries. Beyond a showcase and pitch of product, ElectroCraft is eager to participate in the collaborative discussion of challenges and opportunities that will shape the near and long-term robotic marketplace.