Application of Gantry Robot and Cartesian Robot in Industry
How to choose the right industrial robot? The main selection criteria for industrial robots are the field of application, in automation applications, industrial robots are mainly divided into: Cartesian robots, gantry robots, scara robots, cobot robots, and articulated robots.
How to choose the right industrial robot?
Each robot has its own advantages and disadvantages. They are combined and coordinated with each other in industrial applications to complete various complex actions.
Why choose Cartesian robots or Gantry robots?
Ordinary gantry robots have three axes of XYZ, and can also improve work efficiency by adding linear modules according to different applications. Gantry robots can only move along linear axes so they are very easy to program using a PLC and are ideal for repetitive pick and place, push and other actions.
The main advantage of Cartesian robots is that they can provide high payloads as well as a high level of positioning accuracy throughout the work area. Because of this, the modular structure makes mass production and assembly of large machines possible. In addition, Cartesian robots also have unparalleled precision positioning control, and play an irreplaceable role in photovoltaic panel handling, wafer handling and visual measurement.
Which linear actuator should be used as the arm of a Cartesian robot?
Linear modules are usually divided into 4 types according to the driven model: ball screw driven, belt driven, linear motor, rack and pinion driven. These 4 linear actuators also have different advantages and disadvantages. In practical applications, they are often combined into various Cartesian robots to complete different tasks.
Due to its high-precision positioning advantages, the ball screw linear actuator(HCR series ball screw actuator) is usually used to combine into a desktop robot for dispensing glue, and a three-coordinate measuring instrument for positioning, while a higher-precision steel-based ball screw robot is used for wafer inspection, handling, Such as TPA Robot's KSR, KNR single-axis robot.
The belt actuator has longer stroke and higher load, is usually combined into a gantry robot for palletizers, material pick and place, printing equipment, etc. Rack and pinion actuators are commonly used for seventh-axis robots due to their very long strokes and high loads.
Linear motors have developed rapidly in recent years, and because of their unparalleled precision positioning and long strokes, they are favored by the vast number of automated production islands and combined into various Cartesian robots for photovoltaic panel pick and place, wafer and semiconductor handling , auto parts assembly, precision visual measurement, etc.
TPA Robot is a leading expert in linear motion control solutions in China. We have invested a lot of money in the research and development of linear actuators and automated motion stages. The main products are: linear actuators, direct drive linear motors, single-axis robots, direct drive rotary tables, precision automation stages, cartesian robots, gantry robots.
TPA Robot wins market with our standardized and diversified linear motion products and complete after-sales service system. As the benchmark of China's automatic motion industry, TPA Robot will always provide economical and reliable automatic motion solutions for every demand.
Featured Product
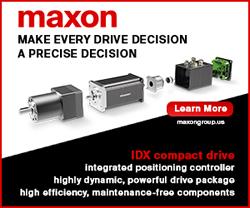
The maxon IDX Compact Drive with Integrated Positioning Controller
The compact brushless EC-i motor combined with an EPOS4 positioning controller delivers a highly dynamic, powerful drive package with field-oriented control (FOC), high efficiency, and maintenance-free components in a high-quality industrial housing. The maxon IDX drives are suitable for use across the entire speed range (from standstill to maximum speed) and have an extremely high overload capability. Together with a positioning controller, the integrated sensor (single turn) enables absolute positioning.