MOBILE MANIPULATORS: WHAT SHOULD I CONSIDER WHEN CHOOSING?
Here you can read which specifications should you consider for choosing the most suitable mobile manipulator for your application and some examlples of tasks that these manipulator robots can automate.
A self-contained mobile manipulator is capable of performing a multitude of meticulous tasks: assembly, welding, material or component handling, screwdriving or polishing. In fact, it could be said that accuracy and repeatability are two of the factors that make the process of automating handling tasks successful.
đź’ˇWHAT BASIC FEATURES OF MOBILE MANIPULATORS SHOULD I TAKE INTO ACCOUNT FOR PRECISION TASKS?
Each application requires specific characteristics, but, in general, for a mobile manipulator aimed at executing precision tasks, it is important to consider these factors:
• Reach: The maximum distance the manipulator arm can reach from its base. This determines the ability of the manipulator arm to access different work areas.
• Positioning accuracy: The ability of the manipulator arm to precisely position its end limb or tool in a specific location within a three-dimensional space. It is crucial for performing tasks that require high precision such as assembling or handling delicate objects.
• Payload: The maximum weight that the manipulator arm can safely carry or handle. In the case of a mobile manipulator robot, it is also worth considering the load capacity of the base, in addition to that of the robotic arm.
• Safety: built-in protection systems, sensors for detecting objects or people, emergency stop systems and other mechanisms to prevent accidents and injuries during operation. Based on this, a mobile manipulator can be qualified as collaborative like the RB-KAIROS+, or not at all.
• Autonomy: period of time during which the industrial manipulator robot can operate independently without the need for loading.
• Ease of use: This refers to how intuitive the control system and user interface of the mobile manipulator is. The ease of use allows operators to program, control, and monitor robot operations as easily as possible.
đź’ˇAPPLICATIONS OF ROBOTNIK MOBILE MANIPULATORS IN DIFFERENT INDUSTRIES
Robotnik's mobile manipulator robots have been developed to perform precision collaborative applications in different industries including automotive, aerospace, agriculture or logistics environments in general.
Some examples of tasks that can be performed by mobile manipulators:
• Material Handling: The mobile handler can pick, transport, and place materials in different locations. For example, moving boxes in a warehouse or sorting components for stock control.
• Machine feeding: supplying raw materials or components to automated machines. For example, feeding a production line with parts in a car factory.
• Screwdriving: The RB-KAIROS+ can integrate different end effectors, such as the OnRobot automatic screwdriver. Thus, it is capable of screwing or unscrewing parts in different locations or fixing components on an assembly line.
• Quality control: The robot can inspect products using sensors or cameras to detect defects or anomalies, or verify the integrity of products on a packaging line.
• Assembly: The manipulator can put different parts together to create complete products, assemble electronic components or machinery parts.
• Welding: Welding operations to join materials are common in any manufacturing environment. RB-KAIROS+ can weld metal components in the manufacture of structures or vehicles.
• Pick & Place: This task involves picking up objects from one location and placing them in another. For example, picking up parts from a conveyor belt and placing them in specific containers.
• Finishing tasks: the final tasks are usually repetitive and very mechanical: polishing, cleaning or labelling products.
Mobile manipulators, in addition to automating tasks in industrial manufacturing environments, are also frequently used for tasks or in environments that pose some level of danger to people.
A mobile robot manipulator can effectively perform a variety of tasks in hazardous environments such as inspecting structures, handling toxic materials, repairing equipment, or handling heavy loads.
In this way, the risk of operator exposure to harmful substances, radiation, harsh environmental conditions or heavy/repetitive tasks is reduced.
Its ability to operate remotely or autonomously allows operators to control manipulators from a safe location, minimizing the risk of exposure.
Ask Robotnik any questions about mobile manipulation.
Featured Product
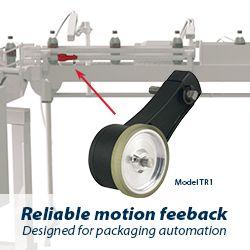
Model TR1 Tru-Trac
The Model TR1 Tru-Trac® linear measurement solution is a versatile option for tracking velocity, position, or distance over a wide variety of surfaces. An integrated encoder, measuring wheel, and spring-loaded torsion arm in one, compact unit, the Model TR1 is easy to install. The spring-loaded torsion arm offers adjustable torsion load, allowing the Model TR1 to be mounted in almost any orientation - even upside-down. The threaded shaft on the pivot axis is field reversible, providing mounting access from either side. With operating speeds up to 3000 feet per minute, a wide variety of configuration options - including multiple wheel material options - and a housing made from a durable, conductive composite material that minimizes static buildup, the Model TR1 Tru-Trac® is the ideal solution for countless applications.