ATI Industrial Automation introduces a high-speed Ethernet Module to enhance robotic tool changer performance
The GBX 10 Gigabit Ethernet Module provides safe and reliable data transmission for advanced automation
Apex, NC, August 28, 2024 - ATI Industrial Automation (ATI) has developed the GBX 10 Gigabit Tool Changer Ethernet Module, designed to allow smart manufacturing processes to optimize performance and flexibility with timely, accurate communication. It excels in high-speed data and signal communication with vision, inspection, metrology, motion control, and fieldbus systems.
Additional features and benefits of ATI's new GBX 10 Gigabit Tool Changer Ethernet Module include:
• Plug-and-play M12 8-pin X-code connectors for safe and reliable pass-through of Cat6/Cat6a industrial Ethernet cables, saving time during integration, with no stripping, crimping, or soldering required.
• Configurable cable exit options between -90°, 0°, and +90° radial positions, allowing users to optimize cable dress and routing to reduce cable strain and maximize system uptime.
• Superior longevity, handling up to one million mating cycles to support applications in advanced industries such as automotive, aerospace, testing, and more.
• Broad compatibility with ATI Standard Tool Changers, Heavy Duty Tool Changers, and Utility Couplers for widespread module standardization.
Learn more at www.ati-ia.com/GBX.
Featured Product
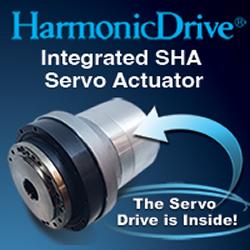
Harmonic Drive - Coming Soon! Integrated Actuators with EtherCAT®!
The IDT Series is a family of compact actuators with an integrated servo drive with
CANopen® and, coming soon, EtherCAT® . With high torque, exceptional
accuracy and repeatability, these actuators eliminate the need for an external drive and
greatly simplify cabling.