Flexxbotics to Present Latest Developments in Advanced Robotic Machine Tending at Automate Trade Show
At the event, Flexxbotics will demonstrate the manufacturing of an electro-mechanical product using an advanced robotic machine tending workcell enabled by Flexxbotics. The demonstration will feature a Universal Robots UR30 collaborative robot with SCHUNK pallet coupling interfacing managing multiple factory machines including a Haas 5-Axis Universal Machining Center, Hexagon Tigo Coordinate Measuring Machine (CMM) and MiJet cleaning station. Flexxbotics solution seamlessly connects the robot to each piece of equipment and coordinates the multi-operation jobs.
Boston, MA - April 30, 2025 - Flexxbotics, delivering digital solutions for robot-driven manufacturing at scale, today announced it will showcase its breakthrough capabilities for advanced robotic machine tending with autonomous process control at Automate 2025 on May 12-15 in Detroit, Michigan.
Flexxbotics solution digitalizes robotic production for next generation smart factory environments. Flexxbotics innovative FlexxCORE™ technology seamlessly connects and coordinates robots with existing automation equipment, IT systems and people. Flexxbotics enables robots to run multiple machines with multiple operations for multiple part SKUs for longer unattended operation in ‘lights out' manufacturing.
At the event, Flexxbotics will demonstrate the manufacturing of an electro-mechanical product using an advanced robotic machine tending workcell enabled by Flexxbotics. The demonstration will feature a Universal Robots UR30 collaborative robot with SCHUNK pallet coupling interfacing managing multiple factory machines including a Haas 5-Axis Universal Machining Center, Hexagon Tigo Coordinate Measuring Machine (CMM) and MiJet cleaning station. Flexxbotics solution seamlessly connects the robot to each piece of equipment and coordinates the multi-operation jobs.
Flexxbotics will be located at Universal Robots Booth #4023 at Automate 2025 with the company's experts on hand throughout the event to discuss automation project details.
"We believe that deploying production robotics at scale is the only way to achieve truly autonomous manufacturing in the smart factory," said Tyler Bouchard, CEO & Co-founder of Flexxbotics. "We will be showcasing our breakthrough FlexxCORE technology for multi-machine robotic interoperability together with UR and our other market leading hardware partners in real-world deployment scenarios at the event."
Automate is the latest robotics and automation event in North America with more than 800 exhibitors and 40,000 attendees. The show brings together innovators from robotics, vision, motion, and AI to showcase the future of advanced manufacturing.
If you have an automation project planned for 2025 and are unable to attend Automate, Flexxbotics has published a white paper titled Complete Guide to Robotic Machine Tending Projects. This paper provides in-depth information on the different aspects of a robot machine tending initiative that are necessary for success. Download the white paper today from: https://flexxboticsinc.com/yckuc4u4.
About Flexxbotics
Flexxbotics enables robot-driven manufacturing at scale. Flexxbotics solution digitalizes robotic production with autonomous process control for next generation smart factory environments. Flexxbotics breakthrough, the unique FlexxCORE™ technology, seamlessly connects and coordinates robots with existing automation equipment, IT systems and people. More powerful, flexible, and open, Flexxbotics revolutionizes the use of robotics in complex production. Visit www.flexxbotics.com to learn more and follow us on LinkedIn.
Featured Product
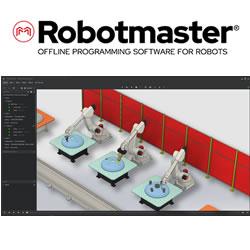