Pipetel's Pipeline Inspection Robots
Pipetel's Explorer is an un-tethered, modular, remotely controllable, self-powered inspection robot for the visual and non-destructive inspection of 6" and 8" natural gas un-piggable transmission pipelines. The most prominent reasons that render a pipeline un-piggable are flow rates that are lower than needed to propel an in-line inspection tool (pig); the presence of obstacles such as valves, mitered bends, back-to-back in and out-of-plane bends; and the cost and operational complications associated with installation of launching and receiving equipment. Explorer can also be used for distribution pipelines as a pre-inspection technology for other rehabilitation and repair techniques.
The Explorer platform uses a Remote Field Eddy Current Sensor (RFEC) which is a non-destructive inspection sensor that uses low frequency alternating current to measure wall thickness for the entire pipe circumference. Explorer also incorporates two fisheye cameras at each end of the robot that provide high quality visual inspection for locating joints, tees and other pipeline appurtenances. As an in-line inspection tool, Explorer is launced operated and retrieved under live conditions and can negotiate diameter changes, bends and tees up to 90° as well as inclined and vertical sections of the pipeline network.
Comments (0)
This post does not have any comments. Be the first to leave a comment below.
Featured Product
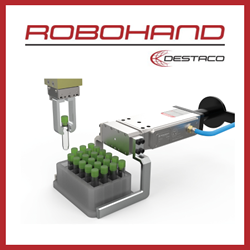