Rethink Robotics releases Baxter, its Manufacturing robot
Baxter, is six feet tall, 300 pounds, and a robot. For a hulking machine, Baxter is remarkably expressive. A pair of eyes on the screen that serves as a face stare down as the robot picks up plastic components, look concerned when it makes a mistake, and direct its glance at its next task when one is finished. It's cute. But the real point of these expressions is that they let workers nearby know instantly if Baxter is performing appropriately, and they provide clues to what it is about to do next. Even more amazing, when Baxter is done with one task, a fellow worker can simply show the robot how to start another. "Almost anyone, literally, can in very short order be shown how to program it," says Chris Budnick, president of Vanguard Plastics. "It's a matter of a couple of minutes."
Baxter is the first of a new generation of smarter, more adaptive industrial robots. Conventional industrial robots are expensive to program, incapable of handling even small deviations in their environment, and so dangerous that they have to be physically separated from human workers by cages. So even as robotics have become commonplace in the automotive and pharmaceutical industries, they remain impractical in many other types of manufacturing. Baxter, however, can be programmed more easily than a Tivo and can deftly respond to a toppled-over part or shifted table. And it is so safe that Baxter's developer, Rethink Robotics, which loaned Baxter to Vanguard Plastics, believes it can work seamlessly alongside its human coworkers.
Comments (0)
This post does not have any comments. Be the first to leave a comment below.
Featured Product
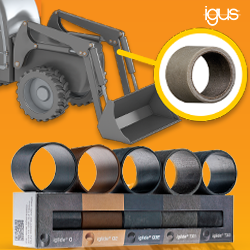