Linkbot Modular Robotic Platform Kickstarter
Each robot has three buttons for user interface and a 3-axis accelerometer. The brain behind all these features is the ATmega128RFA1 by Atmel, running at 16MHz. It integrates an 8-bit AVR microcontroller with an 802.15.4-compliant and ZigBee-capable radio transceiver operating in the 2.4GHz band. Out of the box, it communicates at 250kbps over the air, but with custom firmware you can enable speeds of up to 2Mbps for an 8X increase in throughput.
- Atmel AVR Microcontroller: Compatible with Arduino so you can re-flash with your own firmware using the on-board bootloader
- ZigBee-Capable Radio: Communicate wirelessly with an 802.15.4-compliant radio, create mesh networks, control and monitor remotely
- Multi-Color (RGB) LED: Select from a full spectrum of colors
- 3-Axis Accelerometer: Detect free-falls, bumps, tilt angles
- Buzzer: Play notes or complete tunes, give audio responses to inputs
- RJ11 (6P4C) Expansion Connector: Use a standard phone cable to connect our Bluetooth/breakout boards or your own electronics to your Linkbot's power and I2C bus
- 3x Buttons - Easily control Linkbot modes and functions or write custom functions for button presses
- Micro-USB Connector: Connect to a computer or charger with a standard Micro-USB cable
- Rechargeable Lithium-Ion Battery: Run your Linkbot for over 3 hours for most applications before having to charge
- High Torque:Weight-ratio Motors: Light-but-strong motors produce up to 100oz-in of torque
- Absolute Encoding: Precisely control and measure speeds and angles down to 0.5 degrees
- BaroboLink Software: Graphical interface lets you run programs, actuate motors and read sensors on your computer
- Polycarbonate Housing: Super-durable, drop-tested from second-story building (not recommended) so it can handle your demanding projects
- SnapConnector Mounting Surfaces: Quickly connect and remove wheels, connecting plates, grabbers, even multiple Linkbots; or connect your own accessories with standard screws
Comments (0)
This post does not have any comments. Be the first to leave a comment below.
Featured Product
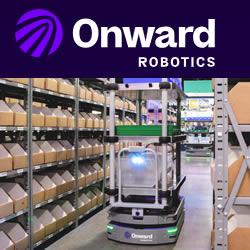
Onward Robotics - Meet Lumabot®
An interactive and powerful autonomous mobile robot for order fulfillment. Lumabot AMRs boost picking productivity and their human counterparts, intelligently moving material to the right person at the right time