Triquad
IEEE Spectrum:
As cool as quadrotors are, in most cases they're simply not as good as helicopters. Because of the way they're designed (with four small rotors instead of one big one), they're less powerful, less efficient, and less maneuverable. The power and efficiency issues come from the fact that one big rotor generates more lift per aircraft footprint than four small rotors, and as for maneuverability, a helicopter that can alter rotor pitch instantly will always outmaneuver a quadrotor that can only control blade speed. Seriously, try doing this with a quadrotor.
So, the thing that quadrotors have going for them is that they're simple. Helicopters have complex main rotor heads, with shafts and bearings and linkages all over the place, while quadrotors just have four motors and that's it. The University of Queensland researchers came up with a "Y4" configuration that aims to take all the good bits of helicopters and make them as simple as quadrotors. I'm just going to start calling this new design a triquad. Keep in mind that this is still a quadrotor: it just had things shifted around a little bit.
Almost all of the triquad's lift comes from its big main fixed-pitch rotor, located at the center of the "Y" (pictured below). The three little fixed-pitch rotors in the "Y" configuration are angled (at a fixed 45 degrees) to provide counter-torque (which they do slightly more efficiently than a helicopter tail rotor) along with pitch and roll control. Here's how the control works... cont'd at IEEE Spectrum
Follow up discussions:
Comments (0)
This post does not have any comments. Be the first to leave a comment below.
Featured Product
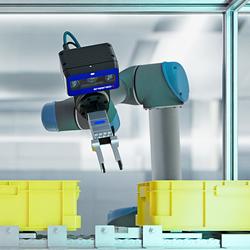