Ino: Command Line Toolkit for Arduino Hardware
Ino tools webpage:
Ino is a command line toolkit for working with Arduino hardware
It allows you to:
- Quickly create new projects
- Build a firmware from multiple source files and libraries
- Upload the firmware to a device
- Perform serial communication with a device (aka serial monitor)
Ino may replace Arduino IDE UI if you prefer to work with command line and an editor of your choice or if you want to integrate Arduino build process to 3-rd party IDE.
Ino is based on make to perform builds. However Makefiles are generated automatically and you’ll never see them if you don’t want to.
Features
- Simple. No build scripts are necessary.
- Out-of-source builds. Directories with source files are not cluttered with intermediate object files.
- Support for *.ino and *.pde sketches as well as raw *.c and *.cpp.
- Support for Arduino Software versions 1.x as well as 0.x.
- Automatic dependency tracking. Referred libraries are automatically included in the build process. Changes in *.h files lead to recompilation of sources which include them.
- Pretty colorful output.
- Support for all boards that are supported by Arduino IDE.
- Fast. Discovered tool paths and other stuff is cached across runs. If nothing has changed, nothing is build.
- Flexible. Support for simple ini-style config files to setup machine-specific info like used Arduino model, Arduino distribution path, etc just once.
(Homepage)
Comments (0)
This post does not have any comments. Be the first to leave a comment below.
Featured Product
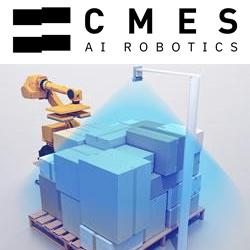
CMES - AI-Powered 3D Robot Vision
Powered by AI, CMES Robotics enables 3D vision for factory robots. CMES AI vision software enables robots to recognize unstructured, flexible, or deformed objects, pick them up, and loading and unloading. CMES Vision software has been deployed worldwide for random palletization and depalletization along with void filling applications. CMES Robotics automates your warehouse, logistics, and supply chain. For more information, please visit: cmesrobotics.com or email info@cmesrobotics.com.