ROBOCHOP: Interactive Installation Allows Internet Users Worldwide to Remotely Control a Pop-up Robotic Plant
From Clemens Weisshaar and Reed Kram:
From March 16-20, 2015 internet users and visitors to CODE_n (Hall 16) at CeBit in Hanover will be able to use an online app connected to the ROBOCHOP installation to design and fabricate a piece of furniture in real time.
The ROBOCHOP interface lets participants instruct a robotic arm to grab and sculpt a prefabricated 40 x 40 x 40cm durable foam cube using a floor mounted hot wire tool to create the object of their choice.
The pop-up robotic plant has been conceptualised, coded and built by KRAM/WEISSHAAR. ROBOCHOP features a needle gripper as the robot’s hand, coaxial cooling of the cutting wire and sensors to measure the wire’s tension and provide direct feedback to the system. This harnesses the robot’s brute force and allows it to sculpt hundreds of unique objects consecutively with elegance and precision. Once manufacturing is complete, each custom object is packaged and posted to the user anywhere in the world entirely free of charge... (full release) (homepage)
Comments (0)
This post does not have any comments. Be the first to leave a comment below.
Featured Product
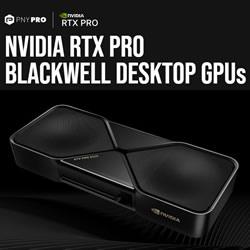