Why Robots and Humans Struggled with DARPA's Challenge

At the DARPA Robotics Challenge, a contest held over the weekend in California, two dozen extremely sophisticated robots did their best to perform a series of tasks on an outdoor course, including turning a valve, climbing some steps, and opening a door (see “A Transformer Wins DARPA’s $2 Million Robotics Challenge”). Although a couple of robots managed to complete the course, others grasped thin air, walked into walls, or simply toppled over as if overcome with the sheer impossibility of it all. At the same time, efforts by human controllers to help the robots through their tasks may offer clues as to how human-machine collaboration could be deployed in various other settings.
“I think this is an opportunity for everybody to see how hard robotics really is,” says Mark Raibert, founder of Boston Dynamics, now owned by Google, which produced an extremely sophisticated humanoid robot called Atlas. Cont'd...
Comments (0)
This post does not have any comments. Be the first to leave a comment below.
Featured Product
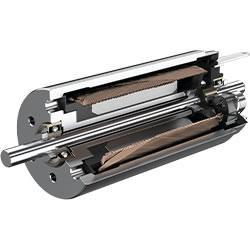
FAULHABER Drive Systems at the Robotics Summit & Expo in Boston from April 30 to May 1 in Hall C at Booth 534
Faulhaber will be presenting their drive systems for robotics and smart technology. Robots are versatile and can be found in many areas, for example, transporting goods, operating on patients or supporting the agriculture industry. With the help of robots, processes can be automated, the flow of materials optimized and employees relieved. Equipped with FAULHABER drive systems, these robots can take on tasks where the demands on function and applications are high.